Self-powered wearable IoT sensors as human-machine interfaces
Abstract
Self-powered wearable Internet of Things (IoT) sensors have made a significant impact on human life and health in recent years. These sensors are known for their convenience, durability, affordability, and longevity, leading to substantial improvements in people’s lives. This review summarizes the development of self-powered wearable IoT sensors in recent years. Materials for self-powered wearable sensors are summarized and evaluated, including nanomaterials, flexible materials, and degradable materials. The working mode of self-powered wearable IoT sensors is analyzed, and the different principles of its physical sensing and chemical sensing are explained. Several common technologies for self-powered wearable IoT sensors are presented, such as triboelectric technology, piezoelectric technology, and machine learning. The applications of self-powered IoT wearable sensors in human-machine interfaces are reviewed. Its current shortcomings and prospects for its future development are also discussed. To conduct this review, a comprehensive literature search was performed using several electronic databases, resulting in the inclusion of 225 articles. The gathered data was extracted, synthesized, and analyzed using a thematic analysis approach. This review provides a comprehensive analysis and summary of its working mode, technologies, and applications and provides references and inspiration for related research in this field. Furthermore, this review also identifies the key directions and challenges for future research.
Keywords
INTRODUCTION
A wearable device is a portable device that is directly worn on the body or integrated into the clothing or accessories of the user[1-3]. It is designed to harvest energy from its environment to power the sensor, typically from sources such as light, heat, or motion[4,5]. In recent years, wearable devices have made rapid progress, which shows great application prospects[6-9]. Some common examples of wearable devices include smartwatches, fitness trackers, virtual and augmented reality headsets, and smart clothing[10,11]. These devices often collect data and communicate with other devices, such as smartphones, to provide users with information, notifications, and other features[11,12]. The advantages of wearable devices are portability and convenience, especially for disease diagnosis. The diagnosis of many diseases requires long-term and continuous monitoring in order to make an accurate assessment. For instance, long-term electrocardiogram (ECG) tests can detect arrhythmia diseases without requiring prolonged hospitalization. This approach can significantly enhance patient comfort[13,14]. Another advantage of wearable devices is their integration. Traditional devices can only complete one function, while wearable devices often integrate multiple functions, for example, the bracelet integrated with blood pressure and pulse monitoring, the monitoring equipment integrated with respiratory intensity frequency and gas component analysis, and the electronic skin integrated with multiple sweat component analysis[15,16]. However, wearable devices are widely used and usually include batteries. The lifespan of a self-powered wearable Internet of Things (IoT) sensor is determined by the capacity and longevity of its battery. If the battery no longer contains any energy, the device will stop working unless it is repaired (battery replacement). In addition, the size of the battery also has a great impact on the size of the sensor device. Therefore, self-powered wearable electronic devices have become one of the important research fields[1,17].
Self-powered wearable devices are wearable devices that are designed to function without the need for an external power source[18-20]. One of the advantages of self-powered wearable devices is convenience. Since no external power supply is required, users can wear the device all day without worrying about charging, which is especially important for the equipment for long-term disease monitoring[21,22]. Self-powered sensors play a prominent role in many cases where it is difficult to charge or replace batteries[23]. From the perspective of environmental protection, since the self-powered devices have no battery, the recycling of this sensor is more environmentally friendly[24,25]. In addition, the use of a battery-free device can also prevent the device with a battery from remaining in place even if the service life of the battery has ended[26]. In some cases, the self-powered devices can extend the service life of the device[27]. However, self-powered wearable devices also have some potential disadvantages. One problem is that their capabilities are limited because the energy-saving technology used to power the device may not support all features and functions of traditional wearable devices[28-30].
Self-powered wearable sensors generate their own power through various mechanisms, such as harvesting energy from the environment, utilizing body heat, or using kinetic energy from motion[30,31]. Self-powered wearable sensors have many potential applications, such as in healthcare, sports, and environmental monitoring[24,32,33]. They offer the advantages of being wireless, autonomous, and unobtrusive, which can lead to more comfortable and convenient monitoring of various parameters[34,35]. There are several types of self-powered wearable sensors, including piezoelectric sensors, thermoelectric sensors, and triboelectric sensors[36-38]. It also has the potential to enable new applications in health monitoring and personalized medicine[24,31,39].
As presented in Figure 1, self-powered wearable sensors can be used in all parts of the human body. These sensors can be used to monitor electroencephalogram (EEG) signals of various brain activities[40]. Using self-powered wearable sensors for EEG measurement can improve the universality of this technology because it allows measurement outside the clinical environment, which is more in line with people’s daily living environment and habits. Additionally, self-powered wearable sensors can monitor respiratory function[41]. They can evaluate respiratory function from many aspects and have the ability to monitor respiration for a long time, evaluate the effectiveness of respiratory therapy, and monitor respiratory function during exercise or sleep. Self-powered wearable sensors also play a great role in ECG measurement[42]. Through long-term monitoring and out-of-hospital monitoring, they can greatly help the overall evaluation of patients. Moreover, these sensors for foot monitoring can be used to monitor foot function and gait mode, providing valuable information about foot and ankle joint function[43]. Furthermore, self-powered wearable sensors can be used to monitor eye movement, provide valuable information about eye function, monitor eye disease, study visual perception and cognition, and track eye movement during tasks requiring visual attention (such as reading or driving)[44]. These sensors can also be used for sweat monitoring, aiding in the diagnosis and management of various conditions such as dehydration, electrolyte imbalance, and skin diseases, and tracking changes in body temperature and metabolic activity[45]. In addition, self-powered wearable sensors for pulse wave monitoring can be used for a variety of applications, such as diagnosis and monitoring of hypertension, assessment of cardiovascular risk, etc.[46]. Lastly, intelligent exoskeletons enable energy collection and angle sensing of joint movements, collecting energy from human joint movements and supplying power to sensors, which can measure joint activity in real time and evaluate joint flexion[47].
Figure 1. Self-powered wearable sensors used in various parts of the human body. They are EEG. Reproduced with permission[40]. Copyright 2015, IOP Publishing Ltd; Breath. Reproduced with permission[41]. Copyright 2019, Elsevier Ltd; ECG. Reproduced with permission[42]. Copyright 2018, American Chemical Society; Feet. Reproduced with permission[43], Copyright 2022, Advanced Materials Technologies; Eyes, Reproduced with permission[44], Copyright 2018, Elsevier Ltd; Sweat, Reproduced with permission[45], Copyright 2022, Elsevier Ltd; Pulses, Reproduced with permission[46] Copyright 2022, Licensee MDPI, Basel, Switzerland; Legs, Reproduced with permission[47] Copyright 2022, American Chemical Society. ECG: Electrocardiogram; EEG: electroencephalogram.
Wearable sensors are IoT devices that can be worn on the body to collect and transmit data about physical activity, vital signs, and other biometric information of the wearer[35,48,49]. They are often used with other IoT devices to create a connected system that can provide real-time monitoring and feedback to the wearer[50,51]. The IoT is a network composed of physical devices, vehicles, household appliances, and other objects embedded in sensors, software, and network connections[52,53]. These devices can connect and exchange data through the Internet, communicate with each other, collect data, and perform operations based on the data. IoT devices are widely used, including in smart homes, wearable devices, industrial automation, transportation, medical care, and agriculture[54,55]. By connecting everyday items to the Internet and collecting data about them, IoT devices can provide valuable insights for optimizing processes, reducing costs, and improving the overall quality of life[49,56].
Compared with previous reviews, this review differs in the following ways[57-60]. First, this review focuses on the application of self-powered wearable IoT sensors as human-machine interfaces rather than just introducing and analyzing their fundamental principles[59,61,62]. We conducted a detailed analysis and discussion of their application scenarios, including electronic skin, fabrics, integrated clothing, etc., and deeply discussed their advantages and disadvantages in these application scenarios and future development directions and challenges. Second, this review provides a more in-depth discussion of the working modes, technologies, and materials used in self-powered wearable IoT sensors. We describe their different physical sensing, chemical sensing, and hybrid sensing modes and introduce the technologies and materials used in them, such as triboelectric nanogenerators (TENGs), piezoelectric nanogenerators (PENGs), etc., for each technology and material detailed analysis and evaluation. Finally, this review combines the latest research progress and practical application scenarios, conducts in-depth discussions and prospects for the future development of this field, and puts forward some guiding suggestions. These suggestions not only provide researchers with research directions and ideas but also provide useful enlightenment and guidance for the industry, which has a certain role in promoting the development of this field.
The overall purpose of this review is to comprehensively sort out and summarize the application of self-powered wearable IoT sensors as human-machine interfaces in order to discuss their development and prospects in the future. With the continuous development and popularization of wearable devices and IoT technology, self-powered sensors, as an emerging technology, have broad application prospects in realizing intelligence, automation, and human-computer interaction. In this context, the purpose of this review is to comprehensively analyze and summarize the progress and innovations achieved in the current research, demonstrate the application of self-powered sensors in the human-machine interface in terms of their role in materials, working modes, technologies used, application scenarios, and advantages, and discuss future development directions and challenges in this field.
Here, the materials of sensors, sensor operation modes, and techniques used in sensors are the focus of our discussion, which are shown in Figure 2. The selection of sensor materials mainly involves degradable materials, flexible materials, and nanomaterials. Degradable materials are of great significance in wearable devices to protect the environment, and under certain conditions, degradable materials are safer and healthier. The use of flexible materials allows the sensor to fit the human body better and provide a more comfortable experience. Nanomaterials, on the other hand, can provide excellent electrical, optical, and mechanical properties, enabling sensors to efficiently and accurately sense and measure various physiological parameters. In terms of the working mode of the sensor, the common ones include chemical, physical, and binding modes. Chemical sensors enable data acquisition primarily by detecting and responding to changes in specific chemicals, such as monitoring the concentration of specific molecules in the blood. Physical sensors focus on measuring physical quantities such as force, temperature, and humidity and converting them into readable electrical signals. Combined modes combine chemical and physical sensing technologies to provide more comprehensive data collection capabilities. The technology in the sensor covers areas such as TENGs, PENGs, and machine learning. The TENG uses the energy generated by mechanical friction to power the sensor, making it self-powered. PENGs use the electrical charge generated by pressure changes to provide electricity. Machine learning technology can effectively analyze complex and multimodal signals, make full use of data, and obtain complete and direct biomedical results. Based on the above information, more advanced and powerful wearable sensors can be realized, providing people with a more intelligent and convenient human-computer interaction experience and promoting the wide application of IoT technology in health monitoring, sports tracking, and other fields.
Figure 2. Main concern of self-powered IoT sensors. Materials of sensors contain flexible materials, Reproduced with permission[38], Copyright 2021, Springer Nature, nanomaterials, Reproduced with permission[106], Copyright 2019, IOP Publishing Ltd, and degradable materials, Reproduced with permission[221]. Copyright 2022, Elsevier Ltd; Sensor operation modes contain physical sensing, Reproduced with permission[222]. Copyright 2018, American Chemical Society, chemical sensing Reproduced with permission[223], Copyright 2022, John Wiley & Sons, Inc., and combined sensing, Reproduced with permission[149], Copyright 2020, American Chemical Society; Techniques in sensors contain TENG Reproduced with permission[224], Copyright 2022, John Wiley & Sons, Inc., PENG, Reproduced with permission[192], Copyright 2023, Elsevier Ltd, and machine learning Reproduced with permission[225], Copyright 2022, John Wiley & Sons, Inc. PENG: Piezoelectric nanogenerator; TENG: triboelectric nanogenerator.
METHODS
Literature search
The objective of this review is to examine the current advancements in self-powered wearable IoT sensors and their potential as human-machine interfaces. The research questions revolve around understanding the state-of-the-art in terms of various types of self-powered wearable IoT sensors, their functionalities, and their diverse applications across different fields. The primary focus is to explore the capabilities and potential of these sensors in enabling seamless interaction between humans and machines. The review concludes by summarizing the key findings and discussing their implications in the field of self-powered wearable IoT sensors as human-machine interfaces. Furthermore, the study addresses their limitations and offers recommendations for future research.
Mainly, but not limited to, multiple electronic databases, including Web of Science and Scopus, were used to conduct a comprehensive literature search. The following keywords were used: “self-powered”, “wearable sensor”, “Internet of Things (IoT)”, and “human-machine interface”. The search string in Web of Science consisted of the following: [“self-powered” OR “wearable sensor” AND “Internet of Things (IoT)” AND “human-machine interface”] with the limitation of (“English language” AND “article”) AND (Publication Year: 2020-2023). Similarly, the search string in Scopus included: TITLE-ABS-KEY[“self-powered” OR “wearable sensor” OR “Internet of Things (IoT)” OR “human-machine interface”] AND {LIMIT-TO[LANGUAGE, “English”] AND LIMIT-TO[DOCTYPE, “ar”] AND [LIMIT-TO(PUBYEAR, 2020-2023)]}. Additionally, there was a search and screening for English articles published between 2010-2020 using a similar search strategy. Web of Science and Scopus databases were selected for the literature search due to their comprehensive coverage of scholarly articles across various disciplines[63-66]. These databases are widely recognized for their extensive indexing and inclusion of high-quality scientific literature[67-71]. By using both Web of Science and Scopus, we aimed to ensure a comprehensive retrieval of relevant articles. Only articles published in English were included to ensure accessibility and readability. Articles directly related to the themes of “self-powered”, “wearable sensor”, “Internet of Things (IoT)”, and “human-machine interface” were considered for inclusion. We focused on articles published between 2020 and 2023 to capture recent developments and up-to-date research. In addition to these criteria, we also excluded duplicate articles and conducted a careful screening of titles and abstracts to assess their alignment with the inclusion criteria. Full-text articles were then retrieved and further evaluated based on the defined criteria.
Literature selection
As illustrated in Supplementary Figure 1, an initial retrieval of 8,096 articles was conducted. These articles underwent a screening process based on their titles and abstracts, resulting in the exclusion of irrelevant articles[72,73]. The full texts of the remaining 305 articles were reviewed in detail to ensure compliance with the inclusion criteria. Articles that were not relevant or did not provide relevant information on self-powered wearable IoT sensors and human-machine interfaces were excluded. A final set of 225 articles was included in the review.
The evaluation process involved reading and excluding articles of low relevance or significance. Only articles aligned with the research content were considered. Relevant information from the selected articles was carefully extracted and organized for subsequent analysis. The data extraction primarily focused on key elements, including technology, applications, advantages, challenges, and future directions. Priority was given to articles that offered in-depth discussions, empirical studies, or novel insights, as they provided valuable contributions to the review. By employing this systematic process of data extraction and synthesis, the review provides a thorough analysis of the current literature on self-powered wearable IoT sensors as human-machine interfaces. This method ensures the comprehensive synthesis of relevant information, identification of trends, and derivation of critical insights, thereby making a significant contribution to the field.
Literature coding
The selected articles underwent comprehensive analysis to extract pertinent data encompassing the types, functions, and applications of self-powered wearable IoT sensors. This information was then organized and categorized into specific topics and categories. Thematic analysis methods were employed to identify the recurring themes, patterns, and distinguishing features across studies. The findings were presented in a clear and concise manner, aligning them with the research question and objectives. The synthesized data were interpreted within the broader context of the review, facilitating a comprehensive understanding of the subject matter. The discussion delved into key insights, emerging trends, and research gaps in the literature. Critical analysis of connections and contradictions within the data provided a balanced and nuanced evaluation of the existing knowledge. The findings were documented in a clear and concise manner. The literature review section provided an overview of the current state of research on self-powered wearable IoT sensors as human-machine interfaces, including applications, energy harvesting mechanisms, performance evaluation methods, and key findings. This comprehensive analysis of the literature enabled the synthesis of existing knowledge and identification of research gaps in the field.
RESULTS
Our review identified a range of self-powered wearable IoT sensors that can be used as human-machine interfaces, including those that utilize energy harvesting, wireless communication, and data processing technologies. The following themes emerged from our analysis.
Materials for self-powered wearable IoT sensors play a key role in their function as human-machine interfaces. These materials not only need to have the characteristics of being able to convert external energy into electrical energy but also need to be safe, comfortable, and reliable when in contact with the human body. Therefore, proper material selection can significantly improve the performance and user experience of self-powered wearable IoT sensors. Some commonly used materials include transparent conductive materials, flexible substrate materials, energy conversion materials, etc. These materials can not only provide a stable energy source for self-powered sensors but also make the sensors softer, more transparent, and more comfortable for wider applications, such as healthcare, sports and fitness, and virtual reality scenarios.
The working modes of self-powered wearable IoT sensors as human-machine interfaces mainly include physical sensing, chemical sensing, and hybrid sensing. Physical sensing uses physical effects to convert external energy (such as pressure, heat, light, etc.) into electrical energy, such as piezoelectric materials and pyroelectric materials; chemical sensing uses chemical reactions to generate electrical energy, such as biofuel cells and microfuel batteries; hybrid sensing is the combination of multiple energy conversion modes, such as combining solar panels and piezoelectric materials. The combination of these working modes can effectively improve the energy utilization efficiency and service life of the sensor so that it can be applied in a wider range of application scenarios. At the same time, these working modes also provide more flexible and innovative ideas for the design and manufacture of sensors, which will help promote the development of wearable IoT sensor technology.
The technology used in self-powered wearable IoT sensors as human-machine interfaces includes a variety of advanced technical means, such as TENGs, PENGs, thermoelectric nanogenerators, biofuel cells, solar cells, machine study, etc. These technical means can convert external energy into electrical energy so that the sensor does not need an external power supply, thereby improving the energy utilization efficiency and service life of the sensor. Among them, machine learning can improve the accuracy and reliability of sensors through the analysis and learning of sensor data, making it more widely used in human-machine interfaces. At the same time, the continuous innovation and application of these technical means will also provide a broader space and prospect for the development of wearable IoT sensors.
Self-powered wearable IoT sensors have a wide range of applications as human-machine interfaces, including e-skins, fabrics, and integrated clothing. Electronic skin can integrate sensors into the surface of the human body to realize real-time perception and interaction of the human-machine interface, thus being widely used in medical monitoring, virtual reality, sports, and other fields. In terms of fabrics, sensors can be integrated into smart clothing to monitor and analyze human health, posture, and movement status, which have great application prospects. In addition, integrated clothing is also an important application direction of self-powered wearable IoT sensors. It can integrate sensors into clothing to realize intelligent monitoring and control and has a wide range of commercial and life application prospects. The continuous expansion and innovation of these application fields will provide a broader market and application space for the development of self-powered wearable IoT sensor technology.
Overall, our review highlights the potential of self-powered wearable IoT sensors as human-machine interfaces and identifies several key areas for future research.
DISCUSSION
Materials of sensors
In order to realize various performances of wearable self-powered sensors, the sensor material is carefully designed[74-80]. The materials used in self-powered wearable sensors typically include flexible materials, nanomaterials, and degradable materials[50,81-84].
Flexible materials
Flexible materials are materials that can bend, twist, or deform without breaking[32,74,85]. In the context of wearable technology, flexible materials are commonly used to make wearable devices more comfortable, lightweight, and durable[86,87]. Flexible materials can bend, twist, and deform without breaking. This allows them to fit the body shape of the wearer and provide a comfortable fit[88]. Flexible materials are usually designed for durability and wear resistance which can withstand repeated bending and twisting without losing shape or breaking[89]. What is more, flexible materials are usually light in weight, compact in shape, and comfortable to wear for a long time[90]. Many flexible materials can be stretched under continuous cracking, which is very important for wearable devices that need to move and stretch with the wearer’s body. Some flexible materials, such as textiles, are breathable and allow air to flow[91]. This helps prevent overheating and discomfort. Some flexible materials are designed to be waterproof, which helps protect electronic components from damage caused by exposure to moisture[92]. Some flexible materials, such as thin films, can be transparent or translucent, which is very important for manufacturing displays and other electronic components[93]. Yi et al. showed a self-powered keyboard with biometric recognition capability, which was characterized by extensibility and flexibility[38]. It was a sensor based on fabric and triboelectricity, which can record physiological signals and human percussion input, achieving self-powered operation. Specifically, it can identify individual typing characteristics to achieve the effect of information security. As shown in Figure 3A, Ma et al. manufactured a wearable fuel cell-type self-powered motion intelligent sensor. The sensor used methanol steam as the target fuel and has a core-shell structure. Porous carbon networks were used as catalysts for methanol oxidation and oxygen reduction reactions, while alkaline hydrogels with high conductivity were used as solid electrolytes[94]. They have excellent sensing and mechanical properties and can be used as wearable equipment to supply power for strain sensors. As shown in Figure 3B, Wang et al. developed a hybrid nanogenerator (HNG) composed of triboelectric-electromagnetic for self-powered gas and motion monitoring[95]. It can turn on the light (3W) and charge the smartphone. The Ti3C2Tx MXene/Ag-based sensor driven by the HNG has been prepared for ethanol detection, which has excellent sensitivity to ethanol. At the same time, a flexible sensor based on MXene/Ag is manufactured using the microelectronic printer and electrospinning equipment to monitor joint activity. Wang et al. developed a TENG based on latex and polytetrafluoroethylene to power the gas sensor and detect ammonia at room temperature[96]. The TENG can support a maximum peak power density of
Figure 3. (A and B) Flexible materials, Reproduced with permission[94,95]. Copyright 2021, American Chemical Society; Copyright 2022, Elsevier B.V.; (C-E) Degradable materials, Reproduced with permission[99,101,103]. Copyright 2020, Elsevier B.V.; Copyright 2022, American Chemical Society; Copyright 2022, Elsevier Ltd; (F-H) Nanomaterials, Reproduced with permission[110-112], Copyright 2021, American Chemical Society; Copyright 2023, Elsevier B.V.; Copyright 2022, Author(s). PDMS: Polydimethylsiloxane; PET: polyethylene glycol terephthalate; PVA: poly(vinyl alcohol).
Degradable materials
Degradable materials refer to materials that can be decomposed into simpler components over time through biodegradation or other chemical or physical processes[98]. Degradable materials have many potential advantages, such as reducing waste and reducing environmental impact[99]. Over time, degradable materials can be decomposed into simpler components, thus reducing the impact on the environment. In some applications, degradable materials are safer and healthier than non-degradable materials[100]. For wearable sensors, some sensors need to come into direct contact with the human body, so biosafety is highly valued. Fortunately, most biodegradable materials have good biological safety characteristics due to their inherent properties. Non-degradable materials, such as plastics, can last in the environment for hundreds of years, causing problems such as garbage, pollution, and wildlife damage. Many degradable materials made from renewable resources, such as plant starch or cellulose, can be grown and harvested on a sustainable basis[101]. This reduces the dependence on non-renewable resources used to produce many non-degradable materials, such as fossil fuels. The use of degradable materials can promote the innovation of product design and development, thus producing more sustainable and environmentally friendly new products and applications[102]. Bio-based plastics, such as starch-based plastics, polylactic acid (PLA), and polyhydroxyalkanoate (PHA), have good plasticity and processability and can be made into products of various shapes, sizes, etc. Cellulose and its derivatives, such as cellulose acetate, cellulose nitrate, etc., have good mechanical strength and heat resistance and can be used to make various materials and products. Natural polymer materials, such as starch, chitosan (chitosan), gelatin, protein, etc., have good biocompatibility and bioactivity and can be used in various applications in the medical field. As shown in Figure 3C, Lan et al. reported a new type of advanced flexible ultra-soft elastic transparent material, which provided a unique combination of scalability, extensibility, and enzymatic degradation[101]. Molecular weight, mechanical strength, and degradation rate can be easily adjusted. Based on these characteristics, a self-powered touch sensor for touch sensing and non-contact proximity detection was manufactured. These properties made the flexible electronic equipment degradable, making them more eco-friendly and environmentally friendly. As shown in Figure 3D, Chen et al. prepared magnetic bacterial cellulose of
Biodegradable green electronic materials are materials designed to naturally degrade in the environment, which can reduce electronic waste and pollution. These materials are typically made of biodegradable polymers, such as cellulose, chitosan, or PLA, which come from renewable resources and have a minimal environmental impact[104]. The combination of biodegradable green electronic materials and self-powered sensor technology can generate widely applicable biodegradable self-powered sensors, such as monitoring the health status of patients. There are several methods for manufacturing biodegradable self-powered sensors. One method is to use materials such as cellulose or PLA as substrates for sensors and then combine them with piezoelectric or thermoelectric power generation technology to generate energy. Another method is to use biomaterials such as enzymes or deoxyribonucleic acid (DNA) as sensing elements and then combine them with biodegradable materials to create fully biodegradable sensors.
Nanomaterials
Nanomaterials are a kind of material with a size of a nanometer, which usually refers to materials with a size of fewer than 100 nanometers in at least one dimension[105]. They play an increasingly important role in the development of self-powered wearable sensors[106]. They provide a series of characteristics that can be used to improve the performance and function of these devices[107]. Nanomaterials can be used to improve the sensitivity, selectivity, and response time of the sensor, thus improving the sensing ability of the self-powered wearable sensor. Nanowires, nanoparticles, or nanorods can greatly improve the output capacity to improve[108,109]. As shown in Figure 3F, Roy et al. proposed to peel palladium thiophosphate by mechanical shear force[110]. The key parameters of the equipment, such as light response and response and recovery time, can be controlled by externally applied voltage and analyte concentration. A frequency-dependent selective acetone sensor with ultra-fast response and recovery time of less than one second. As shown in Figure 3G, Singh et al. developed a CeO2/CdS TENG. It can realize the high sensitivity and selective Zi-powered sensing of carbon dioxide[111]. Different nanomaterials were analyzed and characterized, and it was found that type II heterojunction was formed in CeO2 and CdS. The sensor had a fast response speed (the minimum response time and recovery time are 1,835 and 835 ms, respectively) and ultra-high sensitivity (displayed as 30 when the resistance sensor displays 3.96). As shown in Figure 3H, Pan et al. used the electrospinning technology to produce new polyvinylidene fluoride (PVDF)/Ag nanoparticles/MXene composite nanofibers[112]. Due to their material characteristics, they have high piezoelectric properties. This material shows excellent stability and excellent output performance, enabling it to be used for human energy collection and power supply for LED.
Metal oxide nanomaterials have a wide range of applications in sensors, mainly due to their unique physical and chemical properties, which can improve the sensitivity, selectivity, and response speed of sensors. In IoT sensors, metal oxide nanomaterials can be used to manufacture various types of sensors, such as gas sensors, temperature sensors, humidity sensors, pressure sensors, etc.[113]. Taking gas sensors as an example, metal oxide nanomaterials can be used to manufacture sensors that can detect harmful gases, such as carbon dioxide, carbon monoxide, and ammonia. In addition, metal oxide nanomaterials can also be used to manufacture highly sensitive and selective biosensors for detecting biological molecules such as bacteria, viruses, and cancer cells.
Stretchable soft materials
In the previous chapters, the role of flexible materials was mentioned. Compared to flexible materials, stretchable materials have better stretchability and broader applications. These materials play an important role in self-powered wearable IoT sensors because these materials are able to maintain their electrical properties when the sensor is stretched or bent, allowing the sensor to continue to function and generate electricity when it is moved and deformed. The sensors can adapt to the user’s body shape and activity level and continue to function normally under conditions such as deformation, twisting, and stretching. Moreover, stretchable materials adapt to the contours of the body and allow a full range of motion. This makes them ideal for use in wearable sensors that need to be worn for extended periods of time. One key advantage of stretchable materials is their durability and reliability. They can withstand repeated stretching and deformation without breaking or losing their properties. This makes them ideal for use in wearable sensors that need to withstand the wear and tear of everyday use. Additionally, stretchable materials can be designed with a range of sensing properties, such as pressure sensing, strain sensing, and temperature sensing. This versatility allows for the creation of sensors capable of detecting various physiological signals and environmental factors, making them ideal for health monitoring and environmental sensing applications. While Guo et al. demonstrated a stretchable sensor[27], the way it achieves stretchability is not through stretchable materials but rather through stretchable structures. They designed a snake-shaped PVDF strip device that can monitor joint motion and environmental vibration. Wang et al. demonstrated the stretchable, flexible, and wearable TENG[114]. This device can work effectively during stretching or bending processes. It can be used as a wearable self-powered sensor for real-time human motion monitoring, such as knee joint bending and human posture. Wang et al. demonstrated a self-powered frictional tactile sensor with a multi-layer structure of polydimethylsiloxane (PDMS) frictional layer and PDMS/eutectic gallium indium alloy composite electrode[115]. They can be used to detect pulse waves. Overall, the use of stretchable materials in self-powered wearable IoT sensors offers a range of advantages, including improved comfort and fit, durability and reliability, sensing properties, and energy harvesting capabilities. These advantages make stretchable materials ideal for developing next-generation wearable technologies.
Sensor working mode
Self-powered wearable sensors can work in two kinds of sensing modes: physical sensing and chemical sensing. Physical sensing is a self-powered wearable sensor operating in the physical sensing mode, which can measure changes in physical parameters, such as strain, pressure, temperature, humidity, or motion[33,55,96,116-118]. These sensors usually detect changes in physical parameters measured by changes in electrical, magnetic, or optical properties of materials or equipment[119,120]. Chemical sensing is a self-powered wearable sensor operating in the chemical sensing mode, which can detect changes in chemical or biochemical properties, such as the concentration of specific molecules or ions in biological fluids, environmental samples, or gases[121-123]. Some self-powered wearable sensors can work in physical and chemical sensing modes, allowing simultaneous detection of changes in multiple parameters to more comprehensively monitor physiological or environmental conditions[124,125]. The selection of sensing mode depends on the specific application and the parameters to be measured.
Physical sensing
Physical sensing is a type of sensor that involves measuring physical parameters[94,126]. In self-powered wearable sensors, physical sensing is usually achieved by changing the electrical, magnetic, or optical properties of materials or equipment used to detect physical parameters[41]. Physical sensing is a multifunctional sensing mode that can be used in a wide range of applications, from medical care to sports and fitness to environmental monitoring[98]. The selection of physical sensing technology depends on the specific application and physical parameters to be measured[49,95].
Pressure sensing is a sensing mode that can detect pressure and can be used to monitor blood pressure or detect changes in airflow and other applications[24,127,128]. Self-powered wearable sensors for pressure sensing usually use piezoelectric or capacitive materials, which generate electrical signals in response to pressure changes[77,128-131]. As shown in Figure 4A, Tan et al. designed an artificial intelligence-enhanced blood pressure monitoring wristband[46]. The sensor of the wristband is based on the PENG and has a high signal-to-noise ratio of 29.7 dB. Through the deep learning model, the wristband can predict the blood pressure reading with an error of less than 4 mmHg. This wristband can monitor the blood pressure of subjects for three consecutive days.
Figure 4. Physical sensing (A) Pressure sensing, Reproduced with permission[46]. Copyright 2022, Licensee MDPI, Basel, Switzerland; (B-D) Strain sensing, Reproduced with permission[127,134,135]. Copyright 2022, Elsevier Ltd; Copyright 2022, American Chemical Society; Copyright 2021, The Royal Society of Chemistry; (E) Temperature sensing of breath, Reproduced with permission[138], Copyright 2022, Elsevier Ltd; (F and G) Pulse wave sensing, Reproduced with permission[145,146], Copyright 2020, Elsevier Ltd; Copyright 2022, Elsevier Ltd. Al: Aluminium; FEP: fluorinated ethylene propylene; MS: elastic melamine sponge; PA: polyamide; PENG: piezoelectric nanogenerator; PET: polyethylene terephthalate; PLA: polylactic acid; SUPS: self-powered ultrasensitive pulse sensor.
Strain sensing is common in physical sensing. It is used to measure the deformation or strain of materials and can be used to monitor muscle movement, detect the irregularity of gait, or measure the change of body posture[55,106,132,133]. Self-powered wearable sensors for strain sensing usually use piezoelectric materials, which generate electric charges in response to mechanical strain. As shown in Figure 4B, Lee et al. designed a geometrically asymmetric paired electrode TENG[134]. It enhances pressure-induced electrical output through microelectrodes on the microstructure to monitor deformation. As shown in Figure 4C, Wang
Temperature sensing can monitor temperature changes and can be used to monitor heating in medical applications or process temperature in industrial applications[33,37,55,86,136]. Self-powered wearable sensors for temperature sensing usually use thermoelectric materials, which generate electrical signals in response to temperature changes[98,137]. As shown in Figure 4E, He et al. prepared a thermoelectric composite fabric based on carbon nanotubes (CNT)/polyvinylpyrrolidone (PVP) by a simple ultrasonic coating method and further expanded its application in self-powered temperature/strain sensing[138]. PVP could be used to disperse CNT and increase the binding force between fabric and CNT, thus maintaining stable thermoelectric properties under repeated bending and stretching. The self-driven thermoelectric sensor could realize temperature recognition and respiratory monitoring. It also showed an enhanced output signal when stretching. Zhang et al. reported a compressible and stretchable magnetoelectric sensor (CSMS) with an arch air gap, which can realize self-powered breath monitoring driven by exhaled/inhaled breath[139]. High-sensitivity, self-powered, and electromagnetic electrical sensors can be further used as non-invasive, miniaturized, and portable respiratory monitoring systems to warn of potential health risks.
Pulse wave sensors are a type of physical sensor that can detect the heart rate and other cardiovascular parameters of the wearer[140]. In addition to the heart rate, these sensors can also provide information about the wearer’s blood pressure and arterial stiffness[141]. Pulse wave sensors can be integrated into various wearable devices, such as smart watches, fitness trackers, and health monitors[142-144]. As shown in Figure 4F, Xu et al. developed a self-powered ultra-sensitive pulse sensor based on a TENG for non-invasive multi-indicator cardiovascular monitoring. The detailed characteristic peaks in the pulse waveform of the region can be clearly identified[145]. As shown in Figure 4G, Laurila et al. reported the development of a scalable manufacturing process for a highly inconspicuous piezoelectric ultra-thin e-tattoo arterial pulse wave sensor, which only uses transparent and biocompatible polymer-based materials[146]. The performance of the sensor is optimized in many ways to enhance its performance. Through the actual measurement of the radial artery, its ability to detect pulse waves has been proved.
Chemical sensing
Chemical sensing is a type of sensing that involves the detection of chemical or biochemical properties, such as the concentration of specific molecules or ions in biological fluids, environmental samples, or gases[126,147,148]. In self-powered wearable sensors, chemical sensing is usually achieved by using chemical or biochemical recognition elements (such as enzymes, antibodies, or synthetic receptors), which selectively combine and detect target molecules or ions[95,96,149,150].
Biomarker sensing can monitor the changes of the biomarker level in disease diagnosis[60,151]. Self-powered wearable sensors for biomarker sensing usually use antibody-based sensing technology, which selectively combines specific biomarkers and generates measurable electrical signals[36,152-154]. As shown in Figure 5A, Kanokpaka et al. designed a triboelectric sensor based on a self-powered molecularly imprinted polymer[155]. The PVDF/graphene flexible electrode-modified poly (3-aminophenylborate) imprinted lactic acid molecules showed changes in surface properties after the adsorption of lactic acid. When a higher lactic acid concentration is detected, more lactic acid adsorption results in a lower energy barrier and lower potential. Self-powered triboelectric lactic acid sensors can directly supply power to LED lamps without an external power supply and verify the feasibility of wearable sensors on human skin. As shown in Figure 5B, Lv et al. developed a flexible spiral structure of nitrogen-doped carbon cloth-modified MoN and manufactured a flexible all-solid-state asymmetric supercapacitor[86]. After 10,000 cycles and a retention rate of over 90%, it still exhibits excellent electrochemical performance. As shown in Figure 5C, Shajari et al. manufactured a flexible, self-powered, non-evaporation, non-bubble, non-surfactant, and expandable capillary microfluidic device to reliably collect sweat from different parts of the human body[156]. The sensor can detect the cortisol released by sweat glands to monitor people’s psychological stress levels. The sensor was used to obtain the longitudinal and personalized distribution of sweat cortisol in different body positions. As shown in Figure 5D, Gai et al. designed a wireless self-powered wearable sweat analysis system, which effectively converts the mechanical energy of human motion into electrical energy through the HNG module (HNGM)[39]. The HNGM showed stable output characteristics at low frequencies of 15 mA current and 60 V voltage. Through the real-time body sweat analysis provided by HNGM, it had been proven to be able to selectively monitor the biomarkers (Na+ and K+) in sweat and wirelessly transmit the sensing data to the user interface through Bluetooth.
Figure 5. Chemical sensing (A) Sweat sensing, Reproduced with permission[155], Copyright 2022, Elsevier Ltd; (B) Electrochemical sensing, Reproduced with permission[86], Copyright 2021, American Chemical Society; (C and D) Sweat marker sensing, Reproduced with permission[39,156], Copyright 2023, John Wiley & Sons, Inc.; Copyright 2022, John Wiley & Sons, Inc.; (E and F) Glucose sensing, Reproduced with permission[81,161], Copyright 2022, John Wiley & Sons; Inc. Copyright 2022, American Chemical Society; (G) Lactic acid and glucose sensing, Reproduced with permission[162], Copyright 2021, Springer Nature; (H) Ph sensing, Reproduced with permission[163], Copyright 2020, Elsevier B.V. ADC: Analog-to-digital converter; HNGM: hybrid nanogenerator modules; Gox: glucose oxidase; LIG: laser-induced graphene; MFCM: micropig franz cell membrane; PB: prussian blue; PDMS: polydimethylsiloxane; PI: polyimide; PLA: polylactic acid; PTFE: polytetrafluoroethylene; rGO: reduced graphene oxide; SPSC: self-powered solidstate supercapacitors.
Glucose sensing shows the glucose level of patients with diabetes[157,158]. Self-powered wearable sensors for glucose sensing usually use enzyme-based electrochemical sensing technology to convert glucose into measurable electrical signals[81,93,159,160]. As shown in Figure 5E, Bae et al. showed a stretchable and self-powered microfluidic integrated sensor patch, which includes a stretchable non-enzymatic fuel cell-based sweat glucose sensor and a stretchable cotton thread embedded microfluidic device[81]. The anode and cathode electrodes are coated with catalytic nanoporous gold (NPG), and NPG is coated with platinum nanoparticles. The stretchable microfluidic device made by embedding cotton thread into the PDMS channel to achieve weak constant absorption and sweat flow is integrated into the fuel cell structure. A fully stretchable microfluidic integrated self-powered sensor patch shows excellent continuous monitoring of sweat glucose concentration. As shown in Figure 5F, Kil et al. developed a patch-type self-charging supercapacitor, which can measure biological signals through a continuous power supply without a battery[161]. Glucose oxidase coated on the surface of the micro-needle glucose sensor meets glucose in human interstitial fluid. The self-powered glucose sensor can effectively distinguish the normal, prediabetes, and diabetes levels in 0.5 mL solution absorbed in the laboratory skin model. As shown in Figure 5G, Huang et al. report a stretchable self-powered biosensor with an epidermal electronic format that can detect in situ lactate and glucose concentrations in sweat[162]. The microfluidic channel they developed not only effectively collects sweat but also provides excellent mechanical performance and stable performance output even under 30% stretching.
pH sensing can monitor the pH change of biological fluids or environmental samples. Self-powered wearable sensors for pH sensing usually use materials sensitive to pH, such as polymers or nanomaterials, which will change their electrical properties according to the change of pH value. As shown in Figure 5H, Santiago-Malagon et al. described the structure of a self-powered electrochromic device through screen printing, which can be used to determine metabolites in sweat by the naked eye in the form of 3 × 15 mm color strips[163]. The device comprises a lactate oxidase and osmium-polymer-based anode connected to a coplanar 3 × 15 mm Prussian Blue cathode printed over a transparent poly(3,4-ethylenedioxythiophene) polystyrene sulfonate electrode. The sensor displays the concentration of lactic acid in the range of 0-10 mM on the length of the electrochromic display, which has a contrast of 1.43. As a flexible sensor, it can effectively display the lactic acid content in sweat.
Structure/ technique in wearable self-powered sensors
The TENG is a type of energy harvesting technology that can convert mechanical energy into electrical energy[38,164,165]. The triboelectric effect is the generation of electrical charge that occurs when two materials come into contact and then separate. Unlike the traditional electromagnetic generator, the TENG is very effective in collecting low-frequency mechanical energy. TENGs are increasingly being used in wearable self-powered sensors due to their ability to generate electricity from the body motion of a wearer[166]. In a wearable self-powered sensor, TENGs are typically integrated into the device in a way that allows them to harvest energy from the movement of a wearer, such as when the person walks or moves their arms[167]. Additionally, TENGs are highly durable, can be made using low-cost materials, and are environmentally friendly. There are several types of TENG-based self-powered sensors[29,168,169].
TENGs can be integrated into smart gloves or wristbands, where they can harvest energy from the wrist movements of wearers and power the sensors and displays of the devices[77,170,171]. As shown in Figure 6A, Zu et al. developed a fully automatic early warning glove through the unique elastic-arched triboelectric nanogenerator (EA-TENG) and flexible printed circuit technology. EA-TENG is a sustainable self-powered power supply that can generate electricity by a continuous touch of hands or body and can complete a charging process with only five taps. In the absence of an external power supply, it can achieve real-time contactless static monitoring. As shown in Figure 6B, Lee et al. proposed a flexible HNG (FHNG) that combines solar cells, transparent TENG, and PENGs[172]. FHNG can collect energy from all kinds of energy sources in a sustainable way and be used as a wearable self-powered health monitoring device by sensing health information (such as human motion, arterial pulse rate, or respiratory rate) based on electrical output when attached to the human body. As shown in Figure 6C, Li et al. prepared a new polycation-modified carbon point (PCD)-customized PCD/PVA nanocomposite polymer electrolyte (NPE) and used it as the main triboelectric material to build a new fiber TENG (NPE-TENG) based on NPE for the first time[173]. NPE-TENG-based self-powered wearable sensors and smart gloves are developed, which can realize skin-level tactile perception and joint-related activity monitoring in a fast, real-time, and non-invasive manner. As a sustainable power supply, NPE-TENG can drive small electronic devices and light up hundreds of LEDs.
Figure 6. TENG. (A) Warning Gloves, Reproduced with permission[170], Copyright 2021, John Wiley & Sons, Inc.; (B) Healthcare monitoring, Reproduced with permission[172], Copyright 2021, John Wiley & Sons, Inc.; (C) Smart gloves with fibrous energy harvesters, Reproduced with permission[173]. Copyright 2021, John Wiley & Sons, Inc.; (D) Freeze-resistant and stretchable TENG, Reproduced with permission[177]. Copyright 2022, Elsevier Ltd; (E) Microdiamond-patterned TENG, Reproduced with permission[178]. Copyright 2022, John Wiley & Sons, Inc.; (F) Reconfigurable Fiber, Reproduced with permission[179], Copyright 2022, American Chemical Society; (G) Composite materials TENG for motion monitoring, Reproduced with permission[182], Copyright 2022, Elsevier Ltd. EA-TENG: Elastic-arched triboelectric nanogenerator; FEP: fluorinated ethylene propylene; FTENG: fiber triboelectric nanogenerator; ITO: indium-tin oxide; NDL-TENG: nanocomposite-based doublelayered triboelectric nanogenerator; NPE: nanocomposite polymer electrolytes; PCDs: polycation-modified carbon dots; PDMS: polydimethylsiloxane; PET: polyethylene terephthalate; PVA: polyvinyl alcohol; SMDs: surface mounted devices; SPNYs: silverplated nylon yarns; SSR: stainless steel rod.
Clothing, such as shirts, pants, or socks, can be the carrier of TENG sensors to monitor the movement, posture, and other physiological parameters of the wearer[174-176]. As shown in Figure 6D, Zhu et al. developed a wearable, freeze-resistant, and self-powered electroluminescence (EL) system based on the integration of an organic hydrogel-based EL (OH-EL) device and a liquid electrolyte-based single electrode TENG (LE-TENG), in which the OH-EL device based on self-healing and high conductivity organic hydrogel electrode can be directly controlled by LE-TENG[177]. It still has excellent luminous performance under great mechanical deformation and cold conditions. While harvesting the biomechanical energy of slapping and knee/elbow bending, the self-powered EL system worn on different parts of the human body can realize real-time visual display. As shown in Figure 6E, Zhang et al. proposed a new TENG composed of micro-diamond-patterned PDMS (MR-TENG) to improve its performance[178]. The open circuit voltage and short circuit current of MR-TENG reach 81 V and 2.04 μA, respectively. It is 2.7 times and two times the TENG with smooth PDMS (S-TENG). In addition, MR-TENG can not only be used as a self-powered motion sensor to identify human motion status but also be combined with electronic devices to form a self-powered system to power small wearable devices, including screens, watches, and temperature and humidity sensors. As shown in Figure 6F, Zhou et al. introduced the functional and reconfigurable optical fiber TENG for collecting mechanical energy and self-powered sensors[179]. It is mainly composed of hose, wire, and electric heating wires filled with low melting point alloys. It has important applications in tactile sensing and rehabilitation training.
Shoes or other types of footwear can be combined with TENGs, where they can harvest energy from the footsteps of wearers and power sensors that monitor gait, pressure distribution, and other parameters[62,180,181]. As shown in Figure 6G, Rahman et al. prepared a new type of wearable and stretchable multifunctional double-layer TENG by using nanoporous cobalt oxide/silicon and MXene/silicon nanocomposites derived from metal-organic framework[182]. The preparation of materials can improve the charge capture ability and electronegativity, thus obtaining excellent sensitivity. It can be applied to plantar pressure distribution sensor array and self-powered wearable keyboard.
Piezoelectric nanogenerator
Piezoelectric nanogenerators (PENGs) are devices that can convert mechanical energy (such as motion or pressure) into electrical energy[35,183] and are usually used for self-powered wearable sensors because they can generate electricity from the mechanical energy generated by the movement of a wearer[36,184,185].
Sensors based on PENGs can also be manufactured using organic compounds as piezoelectric materials[186,187]. Organic piezoelectric materials, such as PVDF, have many advantages over inorganic materials, such as higher flexibility, biocompatibility, and ease of processing[188]. The organic PENG sensor has shown promising prospects in various applications, such as biomedical sensors, energy collectors, and touch sensors[189]. They have been used to manufacture self-powered wearable devices that can monitor heart rate, respiration, and muscle activity. They can also be used in smart fabrics, where they can be integrated into clothing to generate energy through movement and temperature changes[190]. As shown in Figure 7A, Athira BS developed a high-output flexible PENG based on PVDF-barium titanate (BaTiO3) (ES-PVDF-BT) composite nanofibers[191]. The output of PENGs based on PVDF-BT nanofibers is ten times higher than that of the original PENG devices based on PVDF nanofibers. This new PENG has been proven to be suitable for real-time vibration sensing applications with automatic power supply. As shown in Figure 7B, Su et al. reported a robust super-hydrophobic antibacterial self-powered electric nanogenerator (PENG) sensor[192]. The PENG sensor is composed of a flexible electrospun piezoelectric nanofiber film and a sprayed cross-fingered CNT electrode. Then, the cross-fingered CNT electrode is encapsulated in a cross-linked conformal hydrophobic nano-coat around each individual fiber by an induced chemical vapor deposition (iCVD). The obtained sensors can accurately monitor various human behaviors, such as breathing and different movements. The iCVD nano-coating provides excellent protection for the sensor, with self-cleaning, super-hydrophobicity, and an antibacterial contamination rate of more than 90%. As shown in Figure 7C, Lo et al. fabricated a PENG based on porous nanofibers by near-field electrospinning[193]. The 3D stacked porous nanofiber structure enhances the stress concentration effect so that poly(vinylidene fluoride-co-trifluoroethylene) (PVDF-TrFE) nanofiber can promote higher performance of electrical output. A self-powered foot pressure recognition statistics system and a personal gait biometric recognition system are developed. Through deep learning, the recognition rate of individual sequential gait piezoelectric signals is 86%.
Figure 7. PENG. (A) PVDF-BaTiO3 Nanofiber PENG, Reproduced with permission[191], Copyright 2022, American Chemical Society; (B) Robust super-hydrophobic antibacterial PENG, Reproduced with permission[192], Copyright 2022, Elsevier Ltd; (C) PVDF-TrFE nanofiber PENG, Reproduced with permission[193], Copyright 2021, John Wiley & Sons, Inc.; (D) MXene/Co3O4 composite-based formaldehyde PENG, Reproduced with permission[198]. Copyright 2021, Elsevier B.V.; (E) PZT-SEBS composite elastomer PENG, Reproduced with permission[185], Copyright 2022, American Chemical Society; (F) metal-free perovskite-based PENG, Reproduced with permission[199], Copyright 2022, John Wiley & Sons, Inc. ES: Electrospun; FPCB: flexible printed circuit board; USTB: University of Science and Technology Beijing.
PENG-based sensors can use inorganic piezoelectric materials, such as zinc oxide (ZnO) or lead zirconate titanate (PZT), to convert mechanical energy into electrical energy, which can be used to power sensors and related electronic equipment[194,195]. They can produce high power density, which means they can generate a large amount of electrical energy from a small amount of mechanical energy[196]. Generally speaking, they have high durability and can resist environmental factors such as temperature and humidity[197]. As shown in Figure 7D, Zhang et al. reported the MXene/Co3O4 composite formaldehyde sensor driven by ZnO/MXene nanowire array PENG at room temperature[198]. With the increase of concentration, the sensor shows an obvious response. In addition, the flexible PENG can be used as a wearable device to collect human motion energy. As shown in Figure 7E, Huang used PZT-SEBS (PZT and styrene-ethylene-butene-styrene) composite elastomer to produce a biocompatible piezoelectric electronic skin. High elasticity PENG can not only obtain mechanical energy from the environment but also show excellent sensing performance for a variety of external stimuli. As shown in Figure 7F, Wu et al. further integrated the synthesized metal-free perovskite (MDABCO-NH4I3) into the PENG, which showed high-output voltage and current[199]. The sensor can be used as a self-powered strain sensor for human-computer interface applications or as an external electrical stimulation device.
Other self-powered sensors
In addition to PENGs and TENGs, there are some self-powered technologies that can also be used in wearable sensors, such as thermoelectric material sensors, solar material sensors, etc.
Thermoelectric materials play an important role in self-powered wearable sensors. The thermoelectric material is a material that can directly convert thermal energy into electrical energy. When one end of a thermoelectric sensor is stimulated by heat, the thermoelectric effect generates a voltage, enabling the conversion of thermal energy to electrical energy[42]. Therefore, the application of thermoelectric materials in self-powered wearable sensors can realize the self-power of the sensor and avoid the failure of the sensor due to the exhaustion of the battery. At the same time, thermoelectric sensors can also convert the heat energy generated by the body itself into electrical energy, thereby realizing the recycling of human energy. He et al. prepared a new self-supporting self-powered temperature and strain sensor using a simple droplet casting method[133]. The composite membrane can maintain stable thermoelectric performance after 1,000 washes and can withstand repeated bending and stretching. It can successfully detect temperature changes and strain deformation under self-powered conditions. Wang et al. have developed a self-powered wearable ultraviolet index detector, which is achieved by using a small flexible thermoelectric generator as the power source[26]. Wearable ultraviolet detectors can successfully self-power by collecting human heat.
Solar materials can directly convert the energy in sunlight into electrical energy, so the application of solar materials in self-powered wearable sensors can realize the self-power of the sensors[200]. The solar sensor can drive the sensor by absorbing light energy and converting it into electrical energy in different indoor or outdoor environments so that the sensor has better adaptability and usability. Solar energy materials also have the characteristics of environmental protection and energy saving, realizing environmental protection and energy recycling, which is of great significance in a society that is increasingly concerned about environmental protection and sustainable development. Choi et al. proposed a new wearable self-powered pressure sensor based on the integration of piezoelectric transmission microporous elastomer (PTME) and thin film organic solar cell (OSC)[201]. PTME shows that in response to the applied pressure, the micropores gradually close with compression, resulting in a change in transmittance. The unique optical properties of PTME enable OSC to respond to changes in current caused by pressure, which can be used for detecting the bending/stretching of human fingers, among other applications.
Machine learning
Machine learning is becoming increasingly popular in self-powered IoT sensors as it enables intelligent decision-making without the need for continuous manual input. In self-powered IoT sensors, machine learning algorithms can be used to analyze data from various sensors and make predictions or decisions based on this data. A key benefit of using machine learning in self-powered IoT sensors is that it can make them more autonomous and self-sufficient. By using machine learning algorithms to analyze data and make decisions, these sensors can reduce the need for manual intervention, which is particularly important in applications where access to manual maintenance or resources may be limited. Tan et al. developed a machine learning-based device[202]. The device can realize gesture recognition with a full keyboard and multi-command input. It is based on machine learning algorithms, with a maximum accuracy of 92.6% when recognizing 26 letters. It can be seen that machine learning algorithms have transformed the complex signals collected by sensors into meaningful and practical results. Another advantage of using machine learning in self-powered IoT sensors is that it can help improve their accuracy and reliability. By analyzing a large amount of data and identifying patterns, machine learning algorithms can make highly accurate predictions and decisions even in complex and dynamic environments. Zhang et al. designed a TENG, which can detect and identify liquid leakage[203]. They designed an intelligent detection and recognition system based on big data and machine learning technology to identify different liquids, with a classification accuracy of over 90%. Zhang et al. designed an intelligent mask with a self-powered breathing sensor as the key component[204]. With the help of machine learning algorithms, the accuracy of distinguishing between the healthy group and three groups of chronic respiratory diseases (asthma, bronchitis, and chronic obstructive pulmonary disease) is as high as 95.5%.
One of the challenges of using machine learning in self-powered IoT sensors is the limited resources available in terms of processing power and memory. To solve this problem, algorithms can be optimized for use on low-power devices, and another method is to enhance the output capability of sensors. Another challenge is the need to train data. In self-powered IoT sensors, data collection is usually limited by available energy and storage capacity. This requires better training methods and more efficient sensors for assistance.
Application of human-machine interfacing
Electronic skin
An electronic skin, also known as e-skin, is a soft, stretchable, and ultra-thin material that simulates the properties and functions of human skin[32]. It can detect various stimuli, such as pressure, temperature, humidity, and light, and respond to them in a manner similar to human skin[115,127]. The development of electronic skin is driven by the demand for advanced technologies that can enhance human-computer interaction and improve medical care[205]. Electronic skins have a wide range of potential applications, including artificial limbs, robots, human-computer interfaces, virtual reality, health monitoring, and personalized medical treatment[206]. The combination of electronic skins and self-powered sensors opens up new possibilities for creating intelligent, energy-saving, and self-sustaining equipment and systems. By integrating self-powered sensors into electronic skins, various physiological and environmental parameters can be continuously monitored in real time. It can also generate its own energy from environmental energy (such as body heat, exercise, or sunlight), making the equipment more energy efficient and sustainable[207,208]. By reducing the need for frequent battery replacement, the self-powered electronic skin sensor can make the equipment more cost-effective and conducive to environmental protection[209]. Self-powered electronic skin sensors provide powerful and multifunctional platforms for new equipment and systems[210]. As shown in Figure 8A, Wen et al. developed a crosstalk-free self-powered strain and temperature sensing (SPST) sensor[33]. Using the piezoresistive and thermoelectric effects of a conductive network, SPST sensors can simultaneously detect strain and temperature stimulation and convert them into independent resistance and voltage signals, respectively. The sensor can be further driven by the thermal voltage generated under the temperature difference between human skin and the surrounding environment to realize self-powered temperature and strain sensing. As a wearable electronic device that can be directly connected to the skin, the SPST sensor can accurately detect the tiny movement of the human body in the self-powered mode. As shown in Figure 8B, Shi et al. reported a self-powered sensing flexible, breathable, and antibacterial TENG electronic skin[206]. It can provide excellent thermal and wet comfort and has a significant antibacterial effect on Escherichia coli and Staphylococcus aureus. The sensor can sensitively sense the change of pressure. As shown in Figure 8C, Chen et al. developed a flexible self-powered temperature and pressure dual-function electronic skin based on triboelectric and thermoelectric coupling effects[211]. It can effectively convert temperature and pressure stimuli into two independent voltage signals. The temperature sensing process is driven by the natural temperature gradient, while the pressure detection process is driven by the triboelectric effect. It has potential in wearable health monitoring systems and artificial intelligence perception.
Figure 8. Applications of Human-machine interfacing. (A) Self-powered temperature and strain sensing, Reproduced with permission[33], Copyright 2022, Elsevier B.V.; (B) All-Fiber Electronic Skin, Reproduced with permission[206], Copyright 2021, American Chemical Society; (C) Temperature-pressure electronic skin, Reproduced with permission[211], Copyright 2022, Elsevier Ltd; (D) Ion gel mechanoreceptor, Reproduced with permission[210], Copyright 2021, American Chemical Society; (E) Nanocellulose-based hydrogel for strain sensing, Reproduced with permission[205], Copyright 2021, Elsevier Ltd; (F) Autoluminescent triboelectric fiber, Reproduced with permission[174], Copyright 2022, Elsevier Ltd; (G) Nano/micro aligned fiber, Reproduced with permission[218], Copyright 2022, Elsevier Ltd; (H) Integrated firefighting clothing, Reproduced with permission[175], Copyright 2022, American Chemical Society. AF: Aerogel fiber; CB: carbon black; CNT: carbon nanotubes; CS: chitosan; NW: nanowires; PEDOT: poly (3,4-ethylenedioxythiophene); PSS: poly (styrenesulfonate); PVA: polyvinyl alcohol; PVDF: polyvinylidene fluoride; SFA: self-powered fire alarm; TENG: triboelectric nanogenerator; TIC-AF: thermal-induced conductive aerogel fiber; TPU: thermoplastic polyurethane.
Part of the strong performance of electronic skin is presented in the form of conductive gel[212]. It can improve the quality and reliability of the signal detected by the sensor[161] and reduce the impedance and noise of the signal and improve the accuracy and sensitivity of the measurement[213]. The use of conductive gel can improve the comfort of electronic skin and reduce skin irritation related to the use of electrodes or sensors[214]. As shown in Figure 8D, Chun et al. developed a self-powered, stretchable, and wearable gel mechanoreceptor sensor[210]. Poly (vinylidene fluoride trifluoroethylene) gel was used to realize self-powered systems, and polyvinyl chloride-based elastic gel was used to detect sensing signals based on charge transfer and distribution. The surfaces of all gels were conical to achieve high sensor sensitivity and conformal contact with the target surface. In addition, the developed sensors were used to obtain various biological signals related to the pressure/strain occurring in the human body. As shown in Figure 8E, Wang et al. use cationic nano cellulose (CCNC) to disperse/stabilize graphite carbon nitride, forming CCNC-g-C3N4 complex and in situ free radical polymerization process to prepare ionic conductive hydrogel with high tensile (tough, viscous). The hydrogel shows high sensitivity and can detect human movement, speech, and breath.
Fabric
Wearable self-powered sensors can be integrated into fabrics to create smart textiles that can monitor all aspects of human physiology and activities[38]. Compared with traditional rigid sensors, fabric-based sensors have many advantages, including being more comfortable, flexible, and easier to use[49]. Sensors based on self-powered fabrics can be used to monitor various physiological parameters, such as heart rate, respiration, and muscle activity[215]. They can also be used to track movement, postures, and environmental factors such as temperature and humidity[216]. The energy generated by the sensor can be used to power the sensor itself or charge the battery for later use[217]. As shown in Figure 8F, Li et al. proposed a self-luminescent and energy-collecting triboelectric fiber as a wearable energy supplier, self-powered sensor, and human-machine interface. It includes a conductive wire wrapped in an elastic phosphorescent triboelectric composite, which can be woven into a large-area high-tensile fabric for sustainable power supply. It can convert biomechanical energy into usable electrical energy. It is developed as system-level smart clothing using newly designed optical fiber. As shown in Figure 8G, Zhou designed a waterproof and breathable fabric TENG (CSYF TENG) based on nano/micro-core sheath yarn and used it for energy collection and self-powered humidity and subtle force sensing[218]. Unlike coated yarn, nanofibers are tightly and orderly wrapped around conductive fibers through conjugated electrospinning technology. CSYF TENGs exhibit superior electrical output, excellent durability, and biomechanical pressure sensitivity and become ideal self-powered humidity sensors. The TENG can also be used as a bioenergy harvester, a self-powered micro-force sensor, and a fabric-based electronic skin.
Integrated clothing
Integrated wearable self-powered clothing sensors represent a type of intelligent clothing that combines self-powered sensors to monitor all aspects of human physiology and activities[175,219]. By integrating these sensors into clothing, they offer more powerful functions and improved convenience[220]. As shown in Figure 8H, He et al. developed an ultra-light self-powered fire alarm (SFA) electronic textile based on electrical conductive gel fiber, which includes calcium alginate (CA), Fe3O4 nanoparticles (Fe3O4 NP), and silver nanowires (Ag NW), realizing ultra-sensitive temperature monitoring and energy collection in fire suits[175]. The resulting SFA electronic fire extinguisher is integrated into the fire protection clothing to achieve temperature sensing and repeatable fire alarm functions. In addition, based on SFA electronic fire extinguisher, an automatic fire self-rescue positioning system is further established. Designing wearable self-powered clothing sensors is a comprehensive endeavor that requires consideration of multiple factors. First, the required sensor type, functionality, accuracy, and sensitivity requirements and how they fit together to achieve the desired functionality need to be determined. Secondly, soft, breathable, and comfortable materials suitable for human skin need to be selected, and aspects such as reliability, durability, environmental protection, and cost must be considered. Then, it is necessary to design an energy supply scheme that can meet the energy demand of the sensor, such as solar energy, kinetic energy, chemical energy, etc., and ensure that sufficient energy supply can be maintained during use. In addition, it is also necessary to consider how to design data processing and transmission schemes to transmit data collected by sensors to devices or the cloud for processing and analysis while ensuring data security and privacy. At the same time, ergonomic design also needs to be considered to ensure that the sensor does not cause discomfort to the human body or affect its performance when worn. Interaction design is also an important aspect. It is necessary to consider how to design the way users interact with sensors to improve user experience and usage efficiency. Finally, the manufacturability and cost of the product also need to be considered to ensure that the product can be widely used in the market and remain competitive. Therefore, designing wearable self-powered clothing sensors requires comprehensive trade-offs and designs to meet the needs and requirements of multiple aspects.
Challenges and outlook
Wearable self-powered sensors have made great progress. It has great advantages in convenience and comfort, real-time monitoring, and material reuse. The self-power effect achieved by TENGs, PENGs, and other technologies also plays an important role in medical care, sports, fitness, and environmental monitoring[48]. Wearable self-powered sensors can be used everywhere in the human body, including smart watches, ECG and heart rate monitoring, temperature sensors, respiratory sensors, etc.[21,24]. Due to their wide range of applications, self-powered wearable sensors can play an important role in the IoT. Self-powered wearable sensors can provide a lot of real-time and long-term data for the IoT and realize a more interconnected and data-driven system. With the continuous progress of technology, self-powered wearable sensors and the IoT are expected to continue to develop, bringing innovation and progress. However, the self-powered wearable sensor still has some problems[164].
Self-powered wearable sensors produce insufficient energy. These sensors generate energy through the movement of a wearer or the surrounding environment. Their output performance is often not enough to support all the required electrical equipment. Or the power supply requires a large range of human movement, which limits its use in various environments. Unreliable power supply conditions pose a great challenge to the use of sensors. This will also lead to some other problems. The sensing range of self-powered wearable sensors is often limited due to low power supply. This will result in reduced accuracy and sensitivity. Due to the limited power supply, the self-powered wearable sensor may not be able to transmit data continuously. This may result in delayed or incomplete data transmission, resulting in information loss or incomplete analysis. Due to the low power supply, the response time of the self-powered wearable sensor may be longer. This will delay the detection of changes in physiological or environmental parameters, thus reducing the effectiveness of the sensor. Due to the natural degradation of the materials used in the sensor or the limited capacity of the energy storage device, the life of the self-powered wearable sensor may be limited. Although some sensors have high stability and long service life, their unstable output performance may cause the service life of other devices to decline. The power shortage of self-powered wearable sensors is a major challenge that needs to be solved through the progress of technology and materials science. To solve this problem, there are several methods that can be used. First, add energy storage devices, such as capacitors or batteries, to increase the energy reserve of the sensor, thereby increasing the working time and stability of the sensor. Second, the energy management system of the sensor can be optimized to maximize the use of harvested energy. For example, more efficient energy conversion devices, optimized energy storage, distribution algorithms, etc., can be adopted. In addition, technologies such as sensors and processors with low power consumption can be used to reduce the energy consumption of the sensor, thereby prolonging the working time of the sensor. At the same time, multiple energy sources can be used for joint energy supply, such as solar energy, thermal energy, vibration energy, etc., and they can be integrated to achieve a more reliable energy supply. Finally, managing the operating mode of the sensor is also an effective way to solve the energy shortage problem. The working mode of the sensor can be reasonably adjusted according to needs to avoid energy waste and improve energy utilization. For example, the sensor is only turned on when it needs to be monitored to avoid unnecessary work for a long time. To sum up, in order to solve the problem of insufficient energy generated by self-powered wearable sensors, various methods can be adopted, such as adding energy storage devices, optimizing energy management systems, adopting low-power consumption technologies, using other energy sources in combination, and managing the working modes of sensors.
Another challenge for self-powered wearable sensors is low durability, which will limit the life and reliability of the sensor. Wearable sensors are exposed to various environmental conditions, such as temperature changes, humidity, mechanical stress, and chemical corrosion, which will cause damage to the sensor over time. Material degradation is common to many self-powered sensors composed of polymer materials, which may lead to sensor misalignment or failure. Repeated mechanical stress may also cause damage to the sensor, resulting in sensor failure. The sensor that often works in sweat or wet exhaled gas may fail due to chemical corrosion. For many reasons, the sensor may not be reused, such as health and safety, avoiding cross infection, or the chemical reaction of the sensor is irreversible and cannot be reused. In the future, solutions such as using more durable materials, improved sensor packaging, and better sensor packaging may help improve the durability and reliability of self-powered wearable sensors. In addition, the development of more sustainable and environmentally friendly materials and manufacturing processes can also help reduce the impact of sensors on the environment.
The accuracy and calibration of the self-powered wearable sensor is the key factor in determining the reliability and usefulness of the collected data. In most application scenarios, we need to pay attention to the accuracy and calibration of sensors, which are prone to many problems. Due to changes in the environment or inherent sensor characteristics, self-powered wearable sensors may have calibration drift over time. Manufacturing variations and environmental factors may cause performance differences among multiple sensors, leading to inconsistent data collected by different sensors. Additionally, self-powered wearable sensors may be subject to interference from other sources, such as electromagnetic radiation, or environmental factors, such as humidity or temperature. At present, there is still a lack of standardization in self-powered wearable sensors. Although this is partly because sensors in the high-tech field need time and experience to develop standards, it may still lead to inconsistent data collected between different sensors or different studies. These problems may lead to inaccurate measurement results, reduce the application range of the sensor, or require professionals to adjust before each use. In the future, calibration, validation, and data analysis using standardized protocols may become a solution. Developing more accurate and reliable sensor technology will also help improve the accuracy and reliability of self-powered wearable sensors. In addition, employing reasonable data analysis technology can help solve some problems related to calibration drift, inter-sensor variation, and interference.
CONCLUSIONS
This review summarizes the research progress in the application status, material function, working mode, technical means, and application fields of self-powered wearable IoT sensors in the human-machine interface. Mainly but not limited to using multiple electronic databases such as Web of Science and Scopus to conduct a comprehensive literature search. Through combing and analyzing the literature, this study found that self-powered wearable IoT sensors, as an important technical means of human-machine interfaces, have been widely used in medical monitoring, virtual reality, smart home, and other fields and have great application potential and commercial value. The role of materials in self-powered sensors mainly includes converting external energy into electrical energy, improving energy utilization efficiency, extending service life, and other related aspects. Their working modes include various forms, such as physical sensing, chemical sensing, and hybrid sensing. At the same time, the technical means of self-powered sensors are constantly being innovated and applied, including TENGs, PENGs, thermoelectric nanogenerators, biofuel cells, solar cells, and machine learning. Finally, this study summarizes the application prospects and limitations of self-powered wearable IoT sensors as a human-machine interface, which provides an important reference for further research and application. The limitations of this review mainly include the following parts. Firstly, the data reviewed in this paper mainly come from published academic literature and patents, which may introduce deviations or overlook certain studies. Moreover, most of the included studies are based on experiments conducted under controlled room conditions. Additionally, while this article briefly mentions some relevant technical details and future research directions, it lacks an in-depth discussion on these aspects. These limitations will affect the comprehensiveness and depth of this review and need to be improved and perfected in future research. To sum up, despite the aforementioned limitations, this paper provides a relatively comprehensive and systematic review and analysis of the application of self-powered wearable IoT sensors as human-machine interfaces, which serves as a valuable reference for a certain basis for research and application in related fields. Overall, the self-powered wearable sensor, serving as the human-machine interface in the IoT domain, holds great potential and represents a key focus for future research. Its implementation can greatly improve people’s health and drive transformative changes in their lifestyles in the future.
DECLARATIONS
Authors’ contributionsProposed original conceptualization: Xi Y, Li Z, Fan Y
Investigated the related work: Xi Y, Tan P
Prepared the figures and wrote the article: Xi Y
Revised and corrected article: Xi Y, Tan P
Supervised the manuscript: Li Z, Fan Y
Availability of data and materialsNot applicable.
Financial support and sponsorshipThis study was supported by the National Natural Science Foundation of China (T2125003, 82202075, 82102231), Beijing Natural Science Foundation (JQ20038, L212010), the National Postdoctoral Program for Innovative Talent (BX20220380), and China Postdoctoral Science Foundation (2022M710389). The authors thank everyone who contributed to this work.
Conflicts of interestNot applicable.
Ethical approval and consent to participateNot applicable.
Consent for publicationNot applicable.
Copyright© The Author(s) 2023.
Supplementary MaterialsREFERENCES
1. Liu F, Han J, Qi J, et al. Research and application progress of intelligent wearable devices. Chinese J Anal Chem 2021;49:159-71.
2. Rahmani AM, Szu-han W, Yu-hsuan K, Haghparast M. The internet of things for applications in wearable technology. IEEE Access 2022;10:123579-94.
3. Lyu Q, Gong S, Yin J, Dyson JM, Cheng W. Soft wearable healthcare materials and devices. Adv Healthc Mater 2021;10:e2100577.
4. Karimi-Maleh H, Orooji Y, Karimi F, et al. A critical review on the use of potentiometric based biosensors for biomarkers detection. Biosens Bioelectron 2021;184:113252.
5. Lee S, Kim H, Park MJ, Jeon HJ. Current advances in wearable devices and their sensors in patients with depression. Front Psychiatry 2021;12:672347.
6. Abouzahra M, Ghasemaghaei M. Effective use of information technologies by seniors: the case of wearable device use. Eur J Inf Syst 2022;31:241-55.
7. Jiang D, Shi G. Research on data security and privacy protection of wearable equipment in healthcare. J Healthc Eng 2021;2021:6656204.
8. Yang B, Jiang X, Fang X, Kong J. Wearable chem-biosensing devices: from basic research to commercial market. Lab Chip 2021;21:4285-310.
9. Kim KK, Kim M, Pyun K, et al. A substrate-less nanomesh receptor with meta-learning for rapid hand task recognition. Nat Electron 2023;6:64-75.
10. Nurkahfi GN, Armi N, Mardiana VA, et al. Development of a low-cost wearable device for Covid-19 self-quarantine monitoring system. Public Health Pract 2022;4:100299.
11. Cho S, Ensari I, Weng C, Kahn MG, Natarajan K. Factors affecting the quality of person-generated wearable device data and associated challenges: rapid systematic review. JMIR Mhealth Uhealth 2021;9:e20738.
12. Webster CS, Scheeren TWL, Wan YI. Patient monitoring, wearable devices, and the healthcare information ecosystem. Br J Anaesth 2022;128:756-8.
13. Meng L, Ge K, Song Y, Yang D, Lin Z. Long-term wearable electrocardiogram signal monitoring and analysis based on convolutional neural network. IEEE Trans Instrum Meas 2021;70:1-11.
14. Randazzo V, Ferretti J, Pasero E. Anytime ECG monitoring through the use of a low-cost, user-friendly, wearable device. Sensors 2021;21:6036.
15. Chen C, Jiang J, He W, Lei W, Hao Q, Zhang X. 3D printed high-loading lithium-sulfur battery toward wearable energy storage. Adv Funct Mater 2020;30:1909469.
16. Shu L, Yu Y, Chen W, et al. Wearable emotion recognition using heart rate data from a smart bracelet. Sensors 2020;20:718.
17. Zhang S, Xia Q, Ma S, et al. Current advances and challenges in nanosheet-based wearable power supply devices. iScience 2021;24:103477.
18. Xu C, Song Y, Han M, Zhang H. Portable and wearable self-powered systems based on emerging energy harvesting technology. Microsyst Nanoeng 2021;7:25.
20. Lou Z, Li L, Wang L, Shen G. Recent progress of self-powered sensing systems for wearable electronics. Small 2017;13:1701791.
21. Dai J, Li L, Shi B, Li Z. Recent progress of self-powered respiration monitoring systems. Biosens Bioelectron 2021;194:113609.
22. Parvin D, Hassan O, Oh T, Islam SK. RF energy harvester integrated self-powered wearable respiratory monitoring system. In. IEEE International Instrumentation and Measurement Technology Conference (I2MTC); 2021.
23. Zhao Z, Lu Y, Mi Y, Meng J, Cao X, Wang N. Structural flexibility in triboelectric nanogenerators: a review on the adaptive design for self-powered systems. Micromachines 2022;13:1586.
24. Zheng Y, Omar R, Hu Z, Duong T, Wang J, Haick H. Bioinspired triboelectric nanosensors for self-powered wearable applications. ACS Biomater Sci Eng 2023;9:2087-102.
25. Rubab N, Kim SW. Triboelectric nanogenerators for self-powered sensors. J Sens Sci 2022;31:79-84.
26. Wang Y, Guo X, Shi Y, Mei D. Self-powered wearable ultraviolet index detector using a flexible thermoelectric generator. J Micromech Microeng 2019;29:045002.
27. Guo R, Zhang H, Cao S, Cui X, Yan Z, Sang S. A self-powered stretchable sensor fabricated by serpentine PVDF film for multiple dynamic monitoring. Materials & Design 2019;182:108025.
28. Wang R, Mu L, Bao Y, et al. Holistically engineered polymer-polymer and polymer-ion interactions in biocompatible polyvinyl alcohol blends for high-performance triboelectric devices in self-powered wearable cardiovascular monitorings. Adv Mater 2020;32:e2002878.
29. Zhang D, Wang D, Xu Z, et al. Diversiform sensors and sensing systems driven by triboelectric and piezoelectric nanogenerators. Coord Chem Rev 2021;427:213597.
30. Huo Z, Wei Y, Wang Y, Wang ZL, Sun Q. Integrated self-powered sensors based on 2D material devices. Adv Funct Materials 2022;32:2206900.
31. Lu Y, Lou Z, Jiang K, Chen D, Shen G. Recent progress of self-powered wearable monitoring systems integrated with microsupercapacitors. Mater Today Nano 2019;8:100050.
32. Yang Z, Zhu Z, Chen Z, et al. Recent advances in self-powered piezoelectric and triboelectric sensors: from material and structure design to frontier applications of artificial intelligence. Sensors 2021;21:8422.
33. Wen N, Guan X, Fan Z, et al. A highly stretchable and breathable self-powered dual-parameter sensor for decoupled temperature and strain sensing. Org Electron 2023;113:106723.
34. Guan H, Zhong T, He H, et al. A self-powered wearable sweat-evaporation-biosensing analyzer for building sports big data. Nano Energy 2019;59:754-61.
35. Yang L, Ma Z, Tian Y, Meng B, Peng Z. Progress on self-powered wearable and implantable systems driven by nanogenerators. Micromachines 2021;12:666.
36. Wang D, Zhang D, Li P, Yang Z, Mi Q, Yu L. Electrospinning of flexible poly(vinyl alcohol)/MXene nanofiber-based humidity sensor self-powered by monolayer molybdenum diselenide piezoelectric nanogenerator. Nanomicro Lett 2021;13:57.
37. Chen J, Zhang L, Tu Y, et al. Wearable self-powered human motion sensors based on highly stretchable quasi-solid state hydrogel. Nano Energy 2021;88:106272.
38. Yi J, Dong K, Shen S, et al. Fully fabric-based triboelectric nanogenerators as self-powered human-machine interactive keyboards. Nanomicro Lett 2021;13:103.
39. Gai Y, Wang E, Liu M, et al. A self-powered wearable sensor for continuous wireless sweat monitoring. Small Methods 2022;6:e2200653.
40. Matiko JW, Wei Y, Torah R, et al. Wearable EEG headband using printed electrodes and powered by energy harvesting for emotion monitoring in ambient assisted living. Smart Mater Struct 2015;24:125028.
41. Wang S, Jiang Y, Tai H, et al. An integrated flexible self-powered wearable respiration sensor. Nano Energy 2019;63:103829.
42. Kim CS, Yang HM, Lee J, et al. Self-powered wearable electrocardiography using a wearable thermoelectric power generator. ACS Energy Lett 2018;3:501-7.
43. Du M, Cao Y, Qu X, et al. Hybrid nanogenerator for biomechanical energy harvesting, motion state detection, and pulse sensing. Adv Mater Technol 2022;7:2101332.
44. Meng X, Cheng Q, Jiang X, et al. Triboelectric nanogenerator as a highly sensitive self-powered sensor for driver behavior monitoring. Nano Energy 2018;51:721-7.
45. Hartel MC, Lee D, Weiss PS, Wang J, Kim J. Resettable sweat-powered wearable electrochromic biosensor. Biosens Bioelectron 2022;215:114565.
46. Tan P, Xi Y, Chao S, et al. An artificial intelligence-enhanced blood pressure monitor wristband based on piezoelectric nanogenerator. Biosensors 2022;12:234.
47. Hu B, Xue J, Jiang D, et al. Wearable exoskeleton system for energy harvesting and angle sensing based on a piezoelectric cantilever generator array. ACS Appl Mater Interfaces 2022;14:36622-32.
48. Shao Y, Shen M, Zhou Y, Cui X, Li L, Zhang Y. Nanogenerator-based self-powered sensors for data collection. Beilstein J Nanotechnol 2021;12:680-93.
49. Wu Z, Cheng T, Wang ZL. Self-powered sensors and systems based on nanogenerators. Sensors 2020;20:2925.
50. Huang P, Wen DL, Qiu Y, et al. Textile-based triboelectric nanogenerators for wearable self-powered microsystems. Micromachines 2021;12:158.
51. Xu K, Lu Y, Takei K. Multifunctional skin-inspired flexible sensor systems for wearable electronics. Adv Mater Technol 2019;4:1800628.
52. Qin XM, Zhang GQ. Application of the internet of things. In: 4th International Conference on Machine Vision (ICMV) - Computer Vision and Image Analysis - Pattern Recognition and Basic Technologies. Singapore, SINGAPORE; 2011.
53. Choi W, Kim J, Lee S, Park E. Smart home and internet of things: a bibliometric study. J Clean Prod 2021;301:126908.
54. Yang Y, Guo X, Zhu M, et al. Triboelectric nanogenerator enabled wearable sensors and electronics for sustainable internet of things integrated green earth. Adv Energy Mater 2023;13:2203040.
55. Wen N, Fan Z, Yang S, et al. Highly stretchable, breathable, and self-powered strain-temperature dual-functional sensors with laminated structure for health monitoring, hyperthermia, and physiotherapy applications. Adv Elect Materials 2022;8:2200680.
56. Lu Z, Zhu Y, Jia C, et al. A self-powered portable flexible sensor of monitoring speed skating techniques. Biosensors 2021;11:108.
57. Shi Q, Dong B, He T, et al. Progress in wearable electronics/photonic - moving toward the era of artificial intelligence and internet of things. InfoMat 2020;2:1131-62.
58. Hayashi H, Tsuji T. Human-machine interfaces based on bioelectric signals: a narrative review with a novel system proposal. IEEJ Transactions Elec Engng 2022;17:1536-44.
59. Izadgoshasb I. Piezoelectric energy harvesting towards self-powered internet of things (IoT) sensors in smart cities. Sensors 2021;21:8332.
60. Su Y, Chen G, Chen C, et al. Self-powered respiration monitoring enabled by a triboelectric nanogenerator. Adv Mater 2021;33:e2170277.
61. Gao M, Wang P, Jiang L, et al. Power generation for wearable systems. Energy Environ Sci 2021;14:2114-57.
62. Rahimi Sardo F, Rayegani A, Matin Nazar A, et al. Recent progress of triboelectric nanogenerators for biomedical sensors: from design to application. Biosensors 2022;12:697.
63. Falagas ME, Pitsouni EI, Malietzis GA, Pappas G. Comparison of PubMed, Scopus, Web of Science, and Google Scholar: strengths and weaknesses. FASEB J 2008;22:338-42.
64. Mongeon P, Paul-hus A. The journal coverage of Web of Science and Scopus: a comparative analysis. Scientometrics 2016;106:213-28.
65. Zhu J, Liu W. A tale of two databases: the use of Web of Science and Scopus in academic papers. Scientometrics 2020;123:321-35.
66. Singh VK, Singh P, Karmakar M, Leta J, Mayr P. The journal coverage of Web of Science, Scopus and Dimensions: a comparative analysis. Scientometrics 2021;126:5113-42.
67. Martín-Martín A, Thelwall M, Orduna-Malea E, Delgado López-Cózar E. Google Scholar, Microsoft Academic, Scopus, Dimensions, Web of Science, and OpenCitations’ COCI: a multidisciplinary comparison of coverage via citations. Scientometrics 2021;126:871-906.
68. Wang Q, Waltman L. Large-scale analysis of the accuracy of the journal classification systems of Web of Science and Scopus. J Informetr 2016;10:347-64.
69. AlRyalat SAS, Malkawi LW, Momani SM. Comparing bibliometric analysis using PubMed, Scopus, and Web of Science databases. J Vis Exp 2019.
70. Franceschini F, Maisano D, Mastrogiacomo L. Empirical analysis and classification of database errors in Scopus and Web of Science. J Informetr 2016;10:933-53.
71. Xie L, Chen Z, Wang H, Zheng C, Jiang J. Bibliometric and visualized analysis of scientific publications on atlantoaxial spine surgery based on Web of Science and VOSviewer. World Neurosurg 2020;137:435-442.e4.
72. Antwi-afari MF, Li H, Wong JK, et al. Sensing and warning-based technology applications to improve occupational health and safety in the construction industry: a literature review. Eng Constr Archit Manag 2019;26:1534-52.
73. Asadzadeh A, Arashpour M, Li H, Ngo T, Bab-hadiashar A, Rashidi A. Sensor-based safety management. Automat Constr 2020;113:103128.
74. Zhang W, Zhang Y, Yang G, et al. Wearable and self-powered sensors made by triboelectric nanogenerators assembled from antibacterial bromobutyl rubber. Nano Energy 2021;82:105769.
75. Kamilya T, Park J. Highly sensitive self-powered biomedical applications using triboelectric nanogenerator. Micromachines 2022;13:2065.
76. Yi Q, Pei X, Das P, Qin H, Lee SW, Esfandyarpour R. A self-powered triboelectric MXene-based 3D-printed wearable physiological biosignal sensing system for on-demand, wireless, and real-time health monitoring. Nano Energy 2022;101:107511.
77. Liang H, He Y, Chen M, et al. Self-powered stretchable mechanoluminescent optical fiber strain sensor. Adv Intell Syst 2021;3:2100035.
78. Parrilla M, De Wael K. Wearable self-powered electrochemical devices for continuous health management. Adv Funct Mater 2021;31:2107042.
79. Shi Y, Zhang K, Ding S, et al. A self-powered piezoelectret sensor based on foamed plastic garbage for monitoring human motions. Nano Res 2023;16:1269-76.
80. Kong H, Si P, Li M, et al. Enhanced electricity generation from graphene microfluidic channels for self-powered flexible sensors. Nano Lett 2022;22:3266-74.
81. Bae CW, Chinnamani MV, Lee EH, Lee N. Stretchable non-enzymatic fuel cell-based sensor patch integrated with thread-embedded microfluidics for self-powered wearable glucose monitoring. Adv Materials Inter 2022;9:2200492.
82. Huang J, Hao Y, Zhao M, Li W, Huang F, Wei Q. All-fiber-structured triboelectric nanogenerator via one-pot electrospinning for self-powered wearable sensors. ACS Appl Mater Interfaces 2021;13:24774-84.
83. Zhang W, Liu Q, Chao S, et al. Ultrathin stretchable triboelectric nanogenerators improved by postcharging electrode material. ACS Appl Mater Interfaces 2021;13:42966-76.
84. Lin Y, Long Z, Liang S, Zhong T, Xing L. A wearable exhaling-oxygen-sensing mask based on piezoelectric/gas-sensing coupling effect for real-time monitoring and uploading lung disease information. J Phys D: Appl Phys 2022;55:224001.
85. Tan P, Zhao C, Fan Y, Li Z. Research progress of self-powered flexible biomedical sensors. Acta Phys Sin 2020;69:178704.
86. Lv F, Ma H, Shen L, et al. Wearable helical molybdenum nitride supercapacitors for self-powered healthcare smartsensors. ACS Appl Mater Interfaces 2021;13:29780-7.
87. Zheng C, Xiang L, Jin W, et al. A flexible self-powered sensing element with integrated organic thermoelectric generator. Adv Mater Technol 2019;4:1900247.
88. Wang Y, Zhu W, Deng Y, et al. Self-powered wearable pressure sensing system for continuous healthcare monitoring enabled by flexible thin-film thermoelectric generator. Nano Energy 2020;73:104773.
89. Mo X, Zhou H, Li W, et al. Piezoelectrets for wearable energy harvesters and sensors. Nano Energy 2019;65:104033.
90. Yuan J, Zhu R, Li G. Self-powered electronic skin with multisensory functions based on thermoelectric conversion. Adv Mater Technol 2020;5:2000419.
91. Xiao Y, Shen D, Zou G, et al. Self-powered, flexible and remote-controlled breath monitor based on TiO2 nanowire networks. Nanotechnology 2019;30:325503.
92. Hou X, Zhang S, Yu J, et al. Flexible piezoelectric nanofibers/polydimethylsiloxane-based pressure sensor for self-powered human motion monitoring. Energy Technol 2020;8:1901242.
93. Sun T, Shen L, Jiang Y, et al. Wearable textile supercapacitors for self-powered enzyme-free smartsensors. ACS Appl Mater Interfaces 2020;12:21779-87.
94. Ma H, Liu Q, Cheng P, et al. Wearable motion smartsensors self-powered by core-shell Au@Pt methanol fuel cells. ACS Sens 2021;6:4526-34.
95. Wang D, Zhang D, Tang M, et al. Rotating triboelectric-electromagnetic nanogenerator driven by tires for self-powered MXene-based flexible wearable electronics. Chem Eng J 2022;446:136914.
96. Wang D, Zhang D, Yang Y, Mi Q, Zhang J, Yu L. Multifunctional latex/polytetrafluoroethylene-based triboelectric nanogenerator for self-powered organ-like MXene/metal-organic framework-derived CuO nanohybrid ammonia sensor. ACS Nano 2021;15:2911-9.
97. Zheng S, Wang H, Das P, et al. Multitasking MXene inks enable high-performance printable microelectrochemical energy storage devices for all-flexible self-powered integrated systems. Adv Mater 2021;33:e2005449.
98. Bhanu N, Harikumar ME, Batabyal SK. Self-powered low-range pressure sensor using biopolymer composites. Appl Phys A 2022:128.
99. Gong H, Xu Z, Yang Y, et al. Transparent, stretchable and degradable protein electronic skin for biomechanical energy scavenging and wireless sensing. Biosens Bioelectron 2020;169:112567.
100. Bi S, Han X, Chen Q, et al. Ultralarge curvature and extreme rapid degradable porous wood based flexible triboelectric sensor for physical motion monitoring. Adv Mater Technol 2023;8:2201066.
101. Lan X, Li W, Ye C, et al. Scalable and degradable dextrin-based elastomers for wearable touch sensing. ACS Appl Mater Interfaces 2023;15:4398-407.
102. Morsada Z, Hossain MM, Islam MT, Mobin MA, Saha S. Recent progress in biodegradable and bioresorbable materials: from passive implants to active electronics. Appl Mater Today 2021;25:101257.
103. Chen K, Li Y, Du Z, et al. CoFe2O4 embedded bacterial cellulose for flexible, biodegradable, and self-powered electromagnetic sensor. Nano Energy 2022;102:107740.
104. Zhu J, Wen H, Zhang H, Huang P, Liu L, Hu H. Recent advances in biodegradable electronics- from fundament to the next-generation multi-functional, medical and environmental device. Sustain Mater Technol 2023;35:e00530.
105. Wu M, Wang Y, Gao S, et al. Solution-synthesized chiral piezoelectric selenium nanowires for wearable self-powered human-integrated monitoring. Nano Energy 2019;56:693-9.
106. Wang Y, Wang R, Wan S, et al. Scalable nanomanufacturing and assembly of chiral-chain piezoelectric tellurium nanowires for wearable self-powered cardiovascular monitoring. Nano Futures 2019;3:011001.
107. Lee E, Yoo H. Self-powered sensors: new opportunities and challenges from two-dimensional nanomaterials. Molecules 2021;26:5056.
108. Jeerapan I, Sempionatto JR, Pavinatto A, You JM, Wang J. Stretchable biofuel cells as wearable textile-based self-powered sensors. J Mater Chem A Mater 2016;4:18342-53.
109. Hallfors NG, Alhawari M, Abi Jaoude M, et al. Graphene oxide: nylon ECG sensors for wearable IoT healthcare - nanomaterial and SoC interface. Analog Integr Circ Sig Process 2018;96:253-60.
110. Roy PK, Marvan P, Mazánek V, et al. Self-powered broadband photodetector and sensor based on novel few-layered Pd3(PS4)2 nanosheets. ACS Appl Mater Interfaces 2021;13:30806-17.
111. Singh A, Singh S, Yadav B. Gigantic enhancement in response of heterostructured CeO2/CdS nanospheres based self-powered CO2 gas sensor: a comparative study. Sens Actuators B Chem 2023;377:133085.
112. Pan CT, Dutt K, Kumar A, et al. PVDF/AgNP/MXene composites-based near-field electrospun fiber with enhanced piezoelectric performance for self-powered wearable sensors. Int J Bioprint 2023;9:647.
113. Yoon Y, Truong PL, Lee D, Ko SH. Metal-oxide nanomaterials synthesis and applications in flexible and wearable sensors. ACS Nanoscience Au 2021;2:64-92.
114. Wang S, He M, Weng B, et al. Stretchable and wearable triboelectric nanogenerator based on kinesio tape for self-powered human motion sensing. Nanomaterials 2018;8:657.
115. Wang J, Cui P, Zhang J, et al. A stretchable self-powered triboelectric tactile sensor with EGaIn alloy electrode for ultra-low-pressure detection. Nano Energy 2021;89:106320.
116. He X, Zi Y, Guo H, et al. A highly stretchable fiber-based triboelectric nanogenerator for self-powered wearable electronics. Adv Funct Mater 2017;27:1604378.
117. Cao Y, Yang Y, Qu X, et al. A self-powered triboelectric hybrid coder for human-machine interaction. Small Methods 2022;6:e2101529.
118. Chen H, Song Y, Cheng X, Zhang H. Self-powered electronic skin based on the triboelectric generator. Nano Energy 2019;56:252-68.
119. Sahu M, Hajra S, Panda S, et al. Waste textiles as the versatile triboelectric energy-harvesting platform for self-powered applications in sports and athletics. Nano Energy 2022;97:107208.
120. Ning C, Dong K, Gao W, et al. Dual-mode thermal-regulating and self-powered pressure sensing hybrid smart fibers. Chem Eng J 2021;420:129650.
121. Zhu G, Ren P, Yang J, et al. Self-powered and multi-mode flexible sensing film with patterned conductive network for wireless monitoring in healthcare. Nano Energy 2022;98:107327.
122. Li Z, Zhang M, Zhang Y, Lu T, Zhu W, Zhang Z. P(VDF-TrFE)-based self-sustained monitoring system. IEEE Trans Dielect Electr Insul 2022;29:1771-6.
123. Hossain G, Rahman M, Hossain IZ, Khan A. Wearable socks with single electrode triboelectric textile sensors for monitoring footsteps. Sens Actuator A Phys 2022;333:113316.
124. A S, Gao X, Lu C, et al. self-powered flexible sensor based on triboelectric nanogenerators for noncontact motion sensing. IEEE Sensors J 2022;22:12547-59.
125. Yao K, Liu Y, Li D, et al. Mechanics designs-performance relationships in epidermal triboelectric nanogenerators. Nano Energy 2020;76:105017.
126. Zhu J, Luo G, Peng X, Wen W, Zhang X, Wang S. Visible light mediated self-powered sensing based on target induced recombination of photogenerated carriers. J Hazard Mater 2021;407:124765.
127. Wang L, Tang Y, Li Y, et al. Multifunctional integrated interdigital microsupercapacitors and self-powered iontronic tactile pressure sensor for wearable electronics. ACS Appl Mater Interfaces 2022;14:47136-47.
128. Ma J, Cui Z, Du Y, et al. Wearable fiber-based supercapacitors enabled by additive-free aqueous MXene inks for self-powering healthcare sensors. Adv Fiber Mater 2022;4:1535-44.
129. Zhou B, Chen Y, Hu K, et al. Matrix-addressed crosstalk-free self-powered pressure sensor array based on electrospun isolated PVDF-TrFE cells. Sens Actuators A Phys 2022;347:113993.
130. Lei H, Xiao J, Chen Y, et al. Bamboo-inspired self-powered triboelectric sensor for touch sensing and sitting posture monitoring. Nano Energy 2022;91:106670.
131. Yu J, Chen L, Hou X, et al. Stretchable and skin-conformal piezo-triboelectric pressure sensor for human joint bending motion monitoring. J Materiomics 2022;8:247-56.
132. Gong W, Hou C, Guo Y, et al. A wearable, fibroid, self-powered active kinematic sensor based on stretchable sheath-core structural triboelectric fibers. Nano Energy 2017;39:673-83.
133. He X, Hao Y, He M, Qin X, Wang L, Yu J. Stretchable thermoelectric-based self-powered dual-parameter sensors with decoupled temperature and strain sensing. ACS Appl Mater Interfaces 2021;13:60498-507.
134. Lee S, Park J. Fingerprint-inspired triboelectric nanogenerator with a geometrically asymmetric electrode design for a self-powered dynamic pressure sensor. Nano Energy 2022;101:107546.
135. Li G, Li L, Zhang P, Chang C, Xu F, Pu X. Ultra-stretchable and healable hydrogel-based triboelectric nanogenerators for energy harvesting and self-powered sensing. RSC Adv 2021;11:17437-44.
136. Bai C, Wang Z, Yang S, et al. Wearable electronics based on the gel thermogalvanic electrolyte for self-powered human health monitoring. ACS Appl Mater Interfaces 2021;13:37316-22.
137. Huang J, Gu J, Liu J, et al. Environment stable ionic organohydrogel as a self-powered integrated system for wearable electronics. J Mater Chem A 2021;9:16345-58.
138. He X, Zhang X, Zhang H, et al. Facile fabrication of stretchable and multifunctional thermoelectric composite fabrics with strain-enhanced self-powered sensing performance. Compos Commun 2022;35:101275.
139. Zhang X, Ai J, Zou R, Su B. Compressible and stretchable magnetoelectric sensors based on liquid metals for highly sensitive, self-powered respiratory monitoring. ACS Appl Mater Interfaces 2021;13:15727-37.
140. Zeng X, Deng HT, Wen DL, Li YY, Xu L, Zhang XS. Wearable multi-functional sensing technology for healthcare smart detection. Micromachines 2022;13:254.
141. Shin YE, Park YJ, Ghosh SK, Lee Y, Park J, Ko H. Ultrasensitive multimodal tactile sensors with skin-inspired microstructures through localized ferroelectric polarization. Adv Sci 2022;9:e2105423.
142. Jinno H, Yokota T, Koizumi M, et al. Self-powered ultraflexible photonic skin for continuous bio-signal detection via air-operation-stable polymer light-emitting diodes. Nat Commun 2021;12:2234.
143. Kim Y, Lee J, Hong H, Park S, Ryu W. Self-powered wearable micropyramid piezoelectric film sensor for real-time monitoring of blood pressure. Adv Eng Mater 2023;25:2200873.
144. Wang B, Liu C, Xiao Y, et al. Ultrasensitive cellular fluorocarbon piezoelectret pressure sensor for self-powered human physiological monitoring. Nano Energy 2017;32:42-9.
145. Xu L, Zhang Z, Gao F, et al. Self-powered ultrasensitive pulse sensors for noninvasive multi-indicators cardiovascular monitoring. Nano Energy 2021;81:105614.
146. Laurila M, Peltokangas M, Montero KL, et al. Self-powered, high sensitivity printed e-tattoo sensor for unobtrusive arterial pulse wave monitoring. Nano Energy 2022;102:107625.
147. Sahoo S, Walke P, Nayak SK, Rout CS, Late DJ. Recent developments in self-powered smart chemical sensors for wearable electronics. Nano Res 2021;14:3669-89.
148. Li L, Chen Z, Hao M, et al. Moisture-driven power generation for multifunctional flexible sensing systems. Nano Lett 2019;19:5544-52.
149. Su Y, Wang J, Wang B, et al. Alveolus-inspired active membrane sensors for self-powered wearable chemical sensing and breath analysis. ACS Nano 2020;14:6067-75.
150. Liu Q, Wang XX, Song WZ, et al. Wireless single-electrode self-powered piezoelectric sensor for monitoring. ACS Appl Mater Interfaces 2020;12:8288-95.
151. Xue Z, Wu L, Yuan J, Xu G, Wu Y. Self-powered biosensors for monitoring human physiological changes. Biosensors 2023;13:236.
152. Wang J, Tang F, Wang Y, Lu Q, Liu S, Li L. Self-healing and highly stretchable gelatin hydrogel for self-powered strain sensor. ACS Appl Mater Interfaces 2020;12:1558-66.
153. Li M, Chen J, Zhong W, et al. Large-area, wearable, self-powered pressure-temperature sensor based on 3D thermoelectric spacer fabric. ACS Sens 2020;5:2545-54.
154. Xu S, Fan Z, Yang S, et al. Highly flexible, stretchable, and self-powered strain-temperature dual sensor based on free-standing PEDOT:PSS/carbon nanocoils-poly(vinyl) alcohol films. ACS Sens 2021;6:1120-8.
155. Kanokpaka P, Chang L, Wang B, et al. Self-powered molecular imprinted polymers-based triboelectric sensor for noninvasive monitoring lactate levels in human sweat. Nano Energy 2022;100:107464.
156. Shajari S, Salahandish R, Zare A, et al. MicroSweat: a wearable microfluidic patch for noninvasive and reliable sweat collection enables human stress monitoring. Adv Sci 2023;10:e2204171.
157. Gonzalez-Solino C, Lorenzo MD. Enzymatic fuel cells: towards self-powered implantable and wearable diagnostics. Biosensors 2018;8:11.
158. Zhao J, Lin Y, Wu J, et al. A fully integrated and self-powered smartwatch for continuous sweat glucose monitoring. ACS Sens 2019;4:1925-33.
159. Zhang X, Jing Y, Zhai Q, et al. Point-of-care diagnoses: flexible patterning technique for self-powered wearable sensors. Anal Chem 2018;90:11780-4.
160. Ghoreishizadeh SS, Moschou D, McBay D, et al. Towards self-powered and autonomous wearable glucose sensor. In: 25th IEEE International Conference on Electronics, Circuits and Systems (ICECS). Bordeaux, France; 2018. p. 701-4.
161. Kil HJ, Kim SR, Park JW. A Self-charging supercapacitor for a patch-type glucose sensor. ACS Appl Mater Interfaces 2022;14:3838-48.
162. Huang X, Li J, Liu Y, et al. Epidermal self-powered sweat sensors for glucose and lactate monitoring. Bio-des Manuf 2022;5:201-9.
163. Santiago-Malagón S, Río-Colín D, Azizkhani H, Aller-Pellitero M, Guirado G, Del Campo FJ. A self-powered skin-patch electrochromic biosensor. Biosens Bioelectron 2021;175:112879.
164. Pu X, Zhang C, Wang ZL. Triboelectric nanogenerators as wearable power sources and self-powered sensors. Natl Sci Rev 2023;10:nwac170.
165. Chen C, Chen L, Wu Z, et al. 3D double-faced interlock fabric triboelectric nanogenerator for bio-motion energy harvesting and as self-powered stretching and 3D tactile sensors. Materials Today 2020;32:84-93.
166. Liu C, Wang Y, Zhang N, et al. A self-powered and high sensitivity acceleration sensor with
167. Jiang M, Lu Y, Zhu Z, Jia W. Advances in smart sensing and medical electronics by self-powered sensors based on triboelectric nanogenerators. Micromachines 2021;12:698.
168. Zheng N, Xue J, Jie Y, Cao X, Wang ZL. Wearable and humidity-resistant biomaterials-based triboelectric nanogenerator for high entropy energy harvesting and self-powered sensing. Nano Res 2022;15:6213-9.
169. Chandrasekhar A, Alluri NR, Sudhakaran MSP, Mok YS, Kim SJ. A smart mobile pouch as a biomechanical energy harvester towards self-powered smart wireless power transfer applications. Nanoscale 2017;9:9818-24.
170. Zu L, Liu D, Shao J, et al. A self-powered early warning glove with integrated elastic-arched triboelectric nanogenerator and flexible printed circuit for real-time safety protection. Adv Mater Technol 2022;7:2100787.
171. Cao W, Ouyang H, Xin W, et al. A stretchable highoutput triboelectric nanogenerator improved by MXene liquid electrode with high electronegativity. Adv Funct Mater 2020;30:2004181.
172. Lee T, Kim I, Kim D. Flexible hybrid nanogenerator for self-powered weather and healthcare monitoring sensor. Adv Electron Mater 2021;7:2100785.
173. Li Z, Xu B, Han J, Huang J, Fu H. A polycation-modified nanofillers tailored polymer electrolytes fiber for versatile biomechanical energy harvesting and full-range personal healthcare sensing. Adv Funct Materials 2022;32:2106731.
174. Li L, Chen Y, Hsiao Y, Lai Y.
175. He H, Liu J, Wang Y, et al. An ultralight self-powered fire alarm e-textile based on conductive aerogel fiber with repeatable temperature monitoring performance used in firefighting clothing. ACS Nano 2022;16:2953-67.
176. Zhao J, Wang Y, Song X, Zhou A, Ma Y, Wang X. Flexible triboelectric nanogenerator based on polyester conductive cloth for biomechanical energy harvesting and self-powered sensors. Nanoscale 2021;13:18363-73.
177. Zhu Y, Xia Y, Wu M, Guo W, Jia C, Wang X. Wearable, freezing-tolerant, and self-powered electroluminescence system for long-term cold-resistant displays. Nano Energy 2022;98:107309.
178. Zhang P, Deng L, Zhang H, He J, Fan X, Ma Y. Enhanced performance of triboelectric nanogenerator with micro-rhombic patterned PDMS for self-powered wearable sensing. Adv Materials Inter 2022;9:2201265.
179. Zhou L, Liu D, Ren L, et al. Reconfigurable fiber triboelectric nanogenerator for self-powered defect detection. ACS Nano 2022;16:7721-31.
180. Li W, Song Z, Kong H, et al. An integrated wearable self-powered platform for real-time and continuous temperature monitoring. Nano Energy 2022;104:107935.
181. Jiang D, Ouyang H, Shi B, et al. A wearable noncontact free-rotating hybrid nanogenerator for self-powered electronics. InfoMat 2020;2:1191-200.
182. Rahman MT, Rana SMS, Salauddin M, et al. Silicone-incorporated nanoporous cobalt oxide and MXene nanocomposite-coated stretchable fabric for wearable triboelectric nanogenerator and self-powered sensing applications. Nano Energy 2022;100:107454.
183. Rayegani A, Saberian M, Delshad Z, et al. Recent advances in self-powered wearable sensors based on piezoelectric and triboelectric nanogenerators. Biosensors 2022;13:37.
184. Zhu M, Yi Z, Yang B, Lee C. Making use of nanoenergy from human - nanogenerator and self-powered sensor enabled sustainable wireless IoT sensory systems. Nano Today 2021;36:101016.
185. Huang X, Qin Q, Wang X, et al. Piezoelectric nanogenerator for highly sensitive and synchronous multi-stimuli sensing. ACS Nano 2021;15:19783-92.
186. Chen X, Song Y, Su Z, et al. Flexible fiber-based hybrid nanogenerator for biomechanical energy harvesting and physiological monitoring. Nano Energy 2017;38:43-50.
187. Guan X, Xu B, Gong J. Hierarchically architected polydopamine modified BaTiO3@P(VDF-TrFE) nanocomposite fiber mats for flexible piezoelectric nanogenerators and self-powered sensors. Nano Energy 2020;70:104516.
188. Zhou X, Parida K, Halevi O, et al. All 3D-printed stretchable piezoelectric nanogenerator with non-protruding kirigami structure. Nano Energy 2020;72:104676.
189. Zhang D, Zhang X, Li X, et al. Enhanced piezoelectric performance of PVDF/BiCl3/ZnO nanofiber-based piezoelectric nanogenerator. Eur Polym J 2022;166:110956.
190. Liu L, Guo X, Lee C. Promoting smart cities into the 5G era with multi-field internet of things (IoT) applications powered with advanced mechanical energy harvesters. Nano Energy 2021;88:106304.
191. Athira BS, George A, Vaishna Priya K, et al. High-performance flexible piezoelectric nanogenerator based on electrospun PVDF-BaTiO3 nanofibers for self-powered vibration sensing applications. ACS Appl Mater Interfaces 2022;14:44239-50.
192. Su C, Huang X, Zhang L, et al. Robust superhydrophobic wearable piezoelectric nanogenerators for self-powered body motion sensors. Nano Energy 2023;107:108095.
193. Lo WC, Chen CC, Fuh YK. 3D stacked near-field electrospun nanoporous PVDF-TrFE nanofibers as self-powered smart sensing in gait big data analytics. Adv Mater Technol 2021;6:2000779.
194. Zeng S, Zhang M, Jiang L, et al. Wearable piezoelectric nanogenerators based on core-shell Ga-PZT@GaOx nanorod-enabled P(VDF-TrFE) composites. ACS Appl Mater Interfaces 2022;14:7990-8000.
195. Kumar M, Kumari P. P(VDF-TrFE)/ZnO nanocomposite synthesized by electrospinning: effect of ZnO nanofiller on physical, mechanical, thermal, rheological and piezoelectric properties. Polym Bull 2023;80:4859-78.
196. Deng L, Deng W, Yang T, et al. Flexible lead-free piezoelectric Ba0.94Sr0.06Sn0.09Ti0.91O3/PDMS composite for self-powered human motion monitoring. J Funct Biomater 2023;14:37.
197. Wang N, Daniels R, Connelly L, et al. All-organic flexible ferroelectret nanogenerator with fabric-based electrodes for self-powered body area networks. Small 2021;17:e2103161.
198. Zhang D, Mi Q, Wang D, Li T. MXene/Co3O4 composite based formaldehyde sensor driven by ZnO/MXene nanowire arrays piezoelectric nanogenerator. Sens Actuators B Chem 2021;339:129923.
199. Wu HS, Wei SM, Chen SW, et al. Metal-free perovskite piezoelectric nanogenerators for human-machine interfaces and self-powered electrical stimulation applications. Adv Sci 2022;9:e2105974.
201. Choi J, Kwon D, Kim B, et al. Wearable self-powered pressure sensor by integration of piezo-transmittance microporous elastomer with organic solar cell. Nano Energy 2020;74:104749.
202. Tan P, Han X, Zou Y, et al. Self-powered gesture recognition wristband enabled by machine learning for full keyboard and multicommand input. Adv Mater 2022;34:e2200793.
203. Zhang W, Wang P, Sun K, Wang C, Diao D. Intelligently detecting and identifying liquids leakage combining triboelectric nanogenerator based self-powered sensor with machine learning. Nano Energy 2019;56:277-85.
204. Zhang K, Li Z, Zhang J, et al. Biodegradable smart face masks for machine learning-assisted chronic respiratory disease diagnosis. ACS Sens 2022;7:3135-43.
205. Wang B, Dai L, Hunter LA, et al. A multifunctional nanocellulose-based hydrogel for strain sensing and self-powering applications. Carbohydr Polym 2021;268:118210.
206. Shi Y, Wei X, Wang K, et al. Integrated all-fiber electronic skin toward self-powered sensing sports systems. ACS Appl Mater Interfaces 2021;13:50329-37.
207. Zhang M, Wang W, Xia G, Wang L, Wang K. Self-powered electronic skin for remote human-machine synchronization. ACS Appl Electron Mater 2023;5:498-508.
208. Lin Y, Duan S, Zhu D, Li Y, Wang B, Wu J. Self-powered and interface-independent tactile sensors based on bilayer single-electrode triboelectric nanogenerators for robotic electronic skin. Adv Intell Syst 2023;5:2100120.
209. Zhao Y, Gao W, Dai K, et al. Bioinspired multifunctional photonic-electronic smart skin for ultrasensitive health monitoring, for visual and self-powered sensing. Adv Mater 2021;33:e2102332.
210. Chun KY, Seo S, Han CS. Self-powered, stretchable, and wearable ion gel mechanoreceptor sensors. ACS Sens 2021;6:1940-8.
211. Chen Y, Lei H, Gao Z, et al. Energy autonomous electronic skin with direct temperature-pressure perception. Nano Energy 2022;98:107273.
212. Wu M, Yao K, Li D, et al. Self-powered skin electronics for energy harvesting and healthcare monitoring. Mater Today Energy 2021;21:100786.
213. Guo Y, Chen Z, Yang W, et al. Multifunctional mechanical sensing electronic device based on triboelectric anisotropic crumpled nanofibrous mats. ACS Appl Mater Interfaces 2021;13:55481-8.
214. Liu Q, Jin L, Zhang P, et al. Nanofibrous grids assembled orthogonally from direct-written piezoelectric fibers as self-powered tactile sensors. ACS Appl Mater Interfaces 2021;13:10623-31.
215. Zhu J, Zeng Y, Luo Y, et al. Triboelectric patch based on maxwell displacement current for human energy harvesting and eye movement monitoring. ACS Nano 2022;16:11884-91.
216. Chen C, Zhang L, Ding W, et al. Woven fabric triboelectric nanogenerator for biomotion energy harvesting and as self-powered gait-recognizing socks. Energies 2020;13:4119.
217. Rana SMS, Rahman MT, Zahed MA, et al. Zirconium metal-organic framework and hybridized Co-NPC@MXene nanocomposite-coated fabric for stretchable, humidity-resistant triboelectric nanogenerators and self-powered tactile sensors. Nano Energy 2022;104:107931.
218. Zhou M, Xu F, Ma L, et al. Continuously fabricated nano/micro aligned fiber based waterproof and breathable fabric triboelectric nanogenerators for self-powered sensing systems. Nano Energy 2022;104:107885.
219. Du X, Tian M, Sun G, et al. Self-powered and self-sensing energy textile system for flexible wearable applications. ACS Appl Mater Interfaces 2020;12:55876-83.
220. Liu L, Yang X, Zhao L, et al. Nanowrinkle-patterned flexible woven triboelectric nanogenerator toward self-powered wearable electronics. Nano Energy 2020;73:104797.
221. Zhang H, Yin F, Shang S, et al. A high-performance, biocompatible, and degradable piezoresistive-triboelectric hybrid device for cross-scale human activities monitoring and self-powered smart home system. Nano Energy 2022;102:107687.
222. Wang M, Zhang J, Tang Y, et al. Air-flow-driven triboelectric nanogenerators for self-powered real-time respiratory monitoring. ACS Nano 2018;12:6156-62.
223. Qin Y, Mo J, Liu Y, et al. Stretchable triboelectric self-powered sweat sensor fabricated from self-healing nanocellulose hydrogels. Adv Funct Materials 2022;32:2201846.
224. Mondal R, Hasan MAM, Zhang R, Olin H, Yang Y. Nanogenerators-based self-powered sensors. Adv Mater Technol 2022;7:2200282.
Cite This Article
Export citation file: BibTeX | RIS
OAE Style
Xi Y, Tan P, Li Z, Fan Y. Self-powered wearable IoT sensors as human-machine interfaces. Soft Sci 2023;3:26. http://dx.doi.org/10.20517/ss.2023.13
AMA Style
Xi Y, Tan P, Li Z, Fan Y. Self-powered wearable IoT sensors as human-machine interfaces. Soft Science. 2023; 3(3): 26. http://dx.doi.org/10.20517/ss.2023.13
Chicago/Turabian Style
Xi, Yuan, Puchuan Tan, Zhou Li, Yubo Fan. 2023. "Self-powered wearable IoT sensors as human-machine interfaces" Soft Science. 3, no.3: 26. http://dx.doi.org/10.20517/ss.2023.13
ACS Style
Xi, Y.; Tan P.; Li Z.; Fan Y. Self-powered wearable IoT sensors as human-machine interfaces. Soft. Sci. 2023, 3, 26. http://dx.doi.org/10.20517/ss.2023.13
About This Article
Special Issue
Copyright
Data & Comments
Data
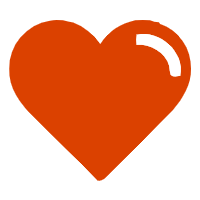

Comments
Comments must be written in English. Spam, offensive content, impersonation, and private information will not be permitted. If any comment is reported and identified as inappropriate content by OAE staff, the comment will be removed without notice. If you have any queries or need any help, please contact us at support@oaepublish.com.