fig6
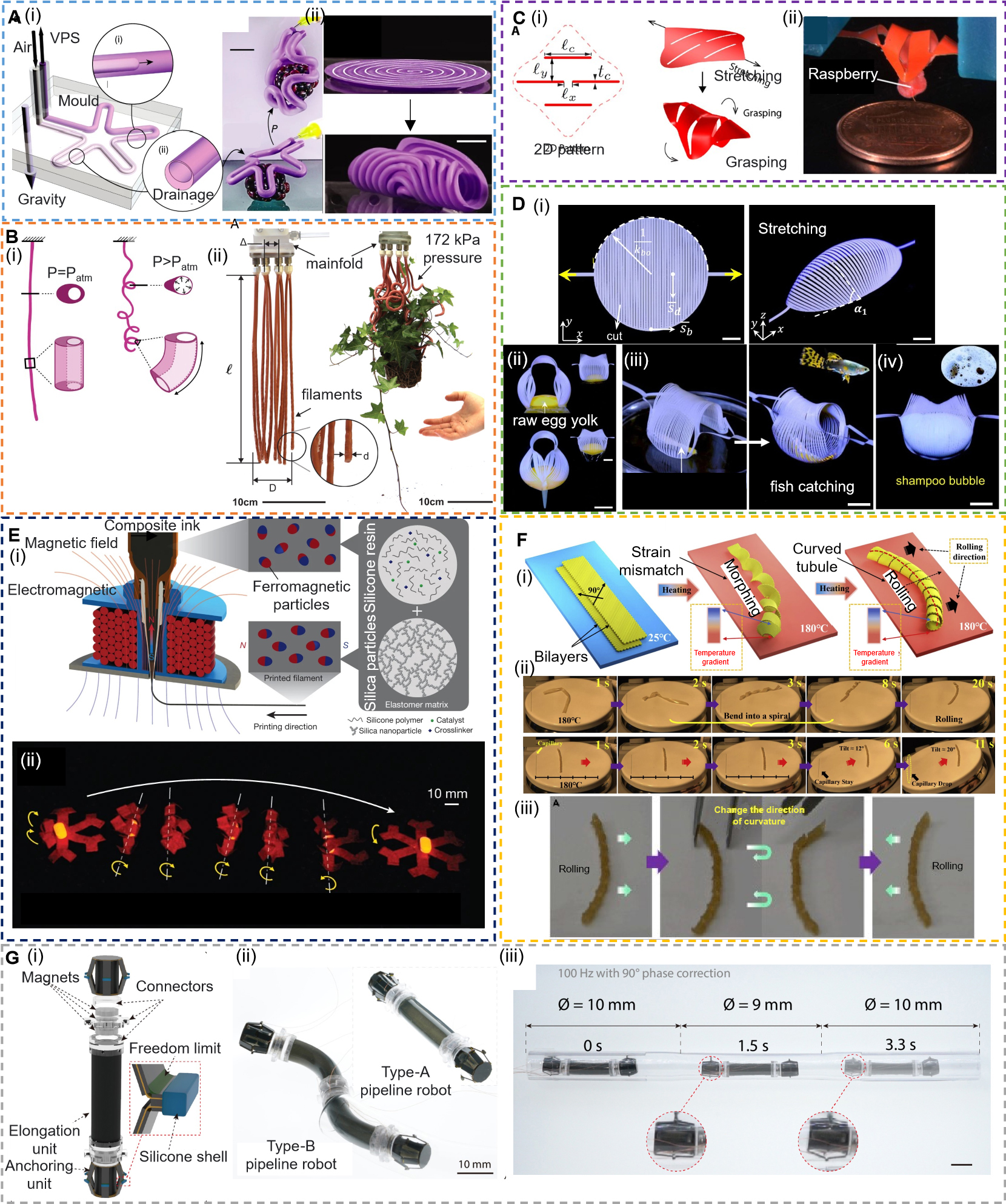
Figure 6. Robotic applications of morphing matter. (A) Soft robots fabricated by bubble casting. (i) Illustration of fabrication processes and demonstration of acting as a gripper; (ii) Spiral-shaped actuator fabricated by bubble casting method. Reproduced with permission from[146]; Copyright 2021, Macmillan Publishers Limited; (B) Entangling filaments. (i) Schematic of the eccentric design of the filaments and their actuating performance; (ii) 12 eccentric hollow filaments grasping a house plant under actuation. Reproduced with permission from[147]; Copyright 2022, National Academy of Sciences, U.S.A; (C) Soft kirigami gripper. (i) Design parameters of the kirigami sheet and its morphing ability under stretching; (ii) Grasping a raspberry using the kirigami gripper. Reproduced with permission from[154]; Copyright 2021, AAAS; (D) Kirigami sheet with prescribed boundaries as soft grippers. (i) 2D precursors before stretching and morphing into a dome shape under stretching; (ii) Grasping raw egg yolk; (iii) Grasping a swimming fish. (iv) Grasping shampoo bubble. Reproduced with permission from[155]; Copyright 2022, Macmillan Publishers Limited; (E) Soft magnetic robot. (i) Schematic of the printing process and the composite ink composition. The magnetic field generated by the permanent magnet/electromagnetic reorients the hard ferromagnetic particles in the soft matrix; (ii) A soft magnetic robot for delivery under magnetic actuation. Reproduced with permission from[156]; Copyright 2018, Macmillan Publishers Limited; (F) A self-propelling thermo-responsive soft robot. (i) Schematic of the printing, morphing, and rolling process on a hot plate; (ii) Morphing process and rolling process on a hot plate; (iii) The rolling direction depends on the curvature direction of the tubule. Reproduced with permission from[157]; Copyright 2021, Cell Press; (G) A pipeline robot. (i) Schematic of the structure of the pipeline robot; (ii) Two different types of pipeline robots. Type A: two anchoring units and one elongation unit. Type B: two elongation units with two anchoring units; (iii) Navigating into a pipe with variable internal diameters (10 to 9 to 10 mm). Reproduced with permisFEMsion from[159]; Copyright 2022, AAAS. FEM: Finite element method.