Liquid metal-based strain-sensing glove for human-machine interaction
Abstract
Soft and stretchable strain sensors have aroused great interest in research and engineering fields due to their promising application potential in many areas, including human-machine interface and healthcare monitoring. However, developing stable, strain-sensitive, and fatigue-resistant wearable strain sensors remains challenging. Herein, we report a low-cost strain-sensing glove based on a commercial nitrile glove and liquid metal as both sensing units and circuit/interconnects, with excellent response to strains and great stability in long-term use. The liquid metal sensing circuit is prepared by scraping the liquid metal slurry in situ on glove fingers, followed by soft silicone encapsulation. The whole process does not involve toxic chemicals, so no strict requirements on the operating environment are necessary. The strain-sensing glove is capable of real-time monitoring of finger gestures in a very sensitive and accurate way, which exhibits great application potential as a soft controller in manipulating the machine hand to achieve related human-machine interaction.
Keywords
INTRODUCTION
With the rapid progress of materials and devices in flexible electronics, wearable electronics are attracting more and more research interests in many fields[1-5], such as healthcare[6,7], sports monitoring[8,9], and human-machine interaction[10-12]. Since wearable devices are mostly put on the limbs that are in motion from time to time, the design and fabrication of strain sensors that can accurately detect motion activities is the key. To date, various soft and stretchable strain sensors have been reported[13,14], including resistive strain sensors based on resistance changes of conductors upon deformation[15], capacitive strain sensors based on changes of structural parameters of soft capacitors[16], and self-powered strain sensors based on triboelectric or piezoelectric mechanisms[17,18]. Although self-powered strain sensors based on triboelectric or piezoelectric nanogenerators can output a voltage signal without relying on an external power supply, such signals are transient, with attenuation issues over time[19]. Resistive and capacitive strain sensors can reflect the strain state in real time, and the maintenance time of the signal depends on the maintenance of the strain state. However, resistive strain sensors possess more straightforward device structures and designs, making them highly suitable for the stable and continuous monitoring of strain states.
Developing flexible resistive strain sensors relies on the design of novel sensing materials, such as carbon nanotubes (CNTs)[20], silver nanowires (Ag NWs)[21], liquid metals[22], and conductive hydrogels[23], which can improve the sensitivity of flexible strain sensors and greatly broaden their manufacturing process. Among them, liquid metals, one of the typical representatives of functional conductive materials, have attracted great interest due to their excellent electrical conductivity and adaptability to various deformations. Most reported liquid metals are associated with the gallium-indium eutectic alloy (EGaIn) and the gallium-indium-tin eutectic alloy (EGaInSn). These alloys can maintain excellent metallic conductivity while changing shapes fluidly under external force at room temperature (~25 °C). As a result, they are considered as good conductive connections and ideal sensing units for deformation in flexible electronics[24]. Additionally, EGaIn and EGaInSn have almost negligible toxicity and low vapor pressure, unlike toxic mercury[25], which allows liquid metals to be utilized in wearable devices with good biocompatibility. To date, taking full advantage of arbitrarily deformable properties of liquid metals, various strategies have been developed for fabricating liquid metal circuits and sensing units[26,27], including microfluidic injection[28], stamp printing[29], 3D printing[30], and so on. However, these methods are always unsatisfactory and poor in applicability when fabricating wearable flexible strain sensors. The issues mainly arise from the complicated and expensive pre-preparation work (preparing microfluidic channel for injection and prototype for stamping printing) and low manufacturing efficiency (3D printing liquid metal circuit line by line), resulting in higher costs and limiting their potential for further commercial production.
To avoid these complicated requirements for the process and fabrication of liquid metal circuits and sensors, a special liquid metal slurry composed of micro/nano-particles (ranging from tens of microns to hundreds of nanometers) has been reported[31-33]. This slurry can solve the typical processing issues caused by surface tension from pure bulk liquid metals, making it easier to print or deposit on a wide range of substrate materials[29,34,35]. However, some subsequent activation operations[36-38] and phase transformation strategies are needed to break the isolation state among liquid metal particles to activate the overall conductivity of liquid metal circuits. The question arises as to whether a general processing route can be developed for such a liquid metal slurry, enabling its use in large-area flexible circuits and sensor arrays on soft substrates.
In this study, we report a general processing strategy of the liquid metal slurry for flexible circuits and sensors. The device demonstrated includes a resistive strain-sensing glove with liquid metal sensing units conformally coated on finger parts, exhibiting excellent strain sensitivity and wearing comfort. The key sensing circuits are realized by scraping the liquid metal slurry on the mask attached to a nitrile glove, and the conductivity of the sensing circuit is activated during the process of peeling off the mask. The liquid metal sensing circuit shows an excellent response to strains (ΔR/R0 ~35% when the strain is 100%), along with stability and fatigue resistance during long-term use. Furthermore, there is no obvious damage even when the temperature is increased by 100 °C. Unlike previously reported liquid metal-based strain sensors fabricated with the help of pre-patterning metal films[39,40] or those fabricated on extra substrates and then fixed on joints[35,41], the strain sensor manufacturing strategy proposed in this manuscript is undoubtedly suitable for large-scale, low-cost, and feasible wearable electronics with a broader range of substrates. For practical demonstration, we used this strain-sensing glove to monitor different finger gestures in real time, effectively displaying even slight gesture changes during this period. Additionally, we manipulated the right machine hand to achieve motions symmetrical to the left hand wearing the strain-sensing glove, potentially offering an alternative to accomplish the task of human-machine collaboration.
EXPERIMENTAL
Preparation of the liquid metal slurry
In this study, we added 10 g liquid metals (EGaIn, Dongguan Huatai Metal Material Technology Co., Ltd.) to 10 g absolute ethanol and sonicated the mixture for ten min (2 s on and 2 s off) with an ultrasonic cell pulverizer (JY92-IIN, Shanghai Huxi Industry Co., Ltd.) to obtain a liquid metal particle dispersion. The liquid metal particle dispersion was left standing in a room environment until obvious stratification occurred. The upper layer of liquid shows a lighter color, and the lower layer is the precipitation composed of the liquid metal particles we need. After we removed the upper layer of the light liquid mixture, 4 mL polyvinyl alcohol (PVA, CAS:9002-89-5, Shanghai Macklin Biochemical Technology Co., Ltd.) aqueous solution (5% w/v) was added to the container and stirred well until a homogeneous liquid metal slurry was obtained.
Fabrication of strain-sensing gloves
Nitrile gloves (Shanghai AMMEX Corporation), commonly used in laboratories, were used as the main body of the strain-sensing glove, acting as the substrate. To prepare a mask for scrape-coating, we first stuck the double-sided adhesive tape (Crown 7972, Shenzhen Xinst Technology Co., Ltd.) on a thin PET film and then used a laser (LPKF ProtoLaser U4) to cut out the desired patterns. Next, we tore off the protective film of the double-sided adhesive tape and directly adhered the entire double-sided adhesive tape to nitrile gloves. Thanks to pressure-sensitive adhesives, such masks exhibited good conformality with the substrate material, which can avoid the leakage of the liquid metal slurry during scraping operation. After the liquid metal slurry was uniformly scraped and coated on the mask, we placed the entire sample in a room environment and allowed the solvent to evaporate entirely, naturally leading to the drying of the slurry. It is worth noting that the liquid metal traces obtained after the solvent evaporates are insulating. However, the inevitable stretching deformation on the glove during the process of tearing off the mask will activate the conductivity of the liquid metal circuit. Subsequently, we encapsulated the liquid metal circuit with a commercial silicone sealant (Kafuter K-705).
Characterization and test methods
We plated the unactivated liquid metal traces, the scratch-activated liquid metal traces, and the stretch-activated liquid metal traces with gold for 60 s using a sputtering system (Quorum Q150T Plus) and then used a scanning electron microscope (SEM) (Quanta™ 450 FEG, FEI Company) to observe and capture surface morphology of these liquid metal traces. Tensile, compression, and fatigue tests performed on liquid metal sensing circuits are realized using a sliding table driven by a stepping motor. In the heating test, we used a hot stage to heat the sample to a specified temperature and kept it at that temperature for a certain period. After the resistance became relatively stable, we measured the resistance of the sample. The resistance of the liquid metal sensing circuit was measured using a multimeter test system (DAQ6510, TEKTRONIX, INC.) in all characterization tests.
RESULTS AND DISCUSSION
Structures and fabrication of the strain-sensing glove
To achieve soft, stretchable, and durable strain sensors for monitoring finger gestures, we designed and fabricated a strain-sensing glove, as shown in Figure 1A. The strain-sensing glove is associated with a three-level structure, including the whole strain-sensing glove, the structure of the strain sensor on a single finger, and components of the liquid metal sensing unit. The SEM image shows the surface morphology of liquid metal sensing circuits, which are formed by interconnected liquid metal particles [Figure 1A]. In this strain-sensing glove, the nitrile glove serves as the substrate of the wearable strain sensor, and the liquid metal is fabricated into circuits and sensing units due to its intrinsic stretchability and ideal conductivity at the metal level, and commercial silicone sealant encapsulates the main deformation parts of liquid metal circuits to protect sensing function. Different from the flexible circuit formed by the bulk liquid metal in previous reports[40,42,43], the strain-sensing circuit in the glove is formed by numerous liquid metal particles stacked together, and the interconnections among liquid metal particles result in good conductivity of the whole circuit when used as macroscopical strain sensors[44]. As shown in Figure 1B, the strain-sensing glove exhibits great flexibility and deformability as a general wearable device, which can withstand different mechanical deformations of twisting, rolling, and stretching.
Figure 1. Soft and stretchable strain-sensing gloves based on liquid metals. (A) Schematic diagram of three-level structures of the strain-sensing glove. Scale bar: 20 μm; (B) Images of the strain-sensing glove in three testing states: twisting, rolling, and stretching. Scale bar: 20 mm; (C) Schematic diagram of the fabrication procedure of the strain-sensing glove.
The fabrication process of the strain-sensing glove is straightforward and low-cost, which is very suitable for commercial mass production, and the entire manufacturing procedure is shown in Figure 1C. First, we used a laser to cut out desired sensing circuit patterns on a mask with pressure-sensitive adhesives. Notably, the pressure-sensitive adhesive is essential for the subsequent scraping operation because it can prevent the liquid metal slurry from leaking into unwanted areas. As previously reported[34,36,45], some natural properties of liquid metals (such as strong fluidity, huge surface tension, etc.) can pose hurdles for processing ideal continuous circuits. However, methods that prepare bulk liquid metals into forms of micro/nano-particles can effectively bypass these intrinsic constraints of liquid metal physical properties on their patterning process[33,46,47]. In this study, we prepared a slurry consisting of liquid metal particles by sonicating bulk liquid metals in absolute ethanol. To prevent circuit cracks after drying, a PVA solution was added to the liquid metal slurry, which served as a binder [Supplementary Figure 1] [35,41]. Then, we scrape-coated the prepared liquid metal slurry on the mask attached to the nitrile glove. After the solvent evaporated completely, we peeled off the mask to obtain an activated conductive liquid metal sensing circuit. Finally, commercial silicone sealant was used as the encapsulation layer for the sensing circuits, which exhibited good ductility to match the nitrile glove substrate after curing. The solvents used in this manufacturing procedure are absolute ethanol and deionized water, causing no harm to the human body and the environment. Therefore, there are no strict requirements on the operating environment, indicating that this strategy for manufacturing a strain-sensing glove has great potential for daily use and mass production.
Activation mechanism of liquid metal circuits
As mentioned above, liquid metal circuits obtained by scraping liquid metal slurries are non-conductive even after the solvent has completely evaporated, which obviously cannot meet the sensing requirements. Therefore, some activation operations are necessary to obtain conductive liquid metal patterns, and the mechanism of mechanically activating the liquid metal circuit to restore its conductivity is shown in Figure 2A. The isolated state of the liquid metal particles is destroyed by external mechanical forces (such as scratching and stretching operations we used in this study), resulting in the interconnections among numerous liquid metal particles, which is manifested as the recovery of the electrical conductivity of liquid metal circuits macroscopically. Notably, the activation effect is permanent and irreversible for restoring the conductivity; that is, once the external force activates the conductivity of circuits, the conductivity of the liquid metal traces will always exist. The optical image of the unactivated traces and the SEM image of corresponding surface morphology are shown in Figure 2B, where the liquid metal particles composing the circuit are isolated from each other, and the traces are insulating. When we gently scratched the surface of the trace with our fingers, the shearing force caused the release of the brightly silvery fresh liquid metal. This caused the connections among liquid metal particles and activated the conductivity of liquid metal traces, as shown in Figure 2C and Supplementary Video 1. In addition to soft contact methods, such as finger scratching, drawing with a sharp object (such as a tweezer tip) on the traces formed by a liquid metal slurry can also activate local conductivity
Figure 2. Mechanical activation of circuits prepared from the liquid metal slurry. (A) Schematic diagram of the mechanical activation mechanism of circuits consisting of numerous stacked liquid metal particles; (B) Optical image of unactivated liquid metal traces and their scanning electron microscope (SEM) image. Scale bar: 5 mm, 50 μm; (C) Optical image of liquid metal traces activated by scratching and SEM image of their surface topography. Scale bar: 5 mm, 100 μm; (D) Optical image of liquid metal traces activated by stretching and SEM image of their surface topography. Scale bar: 5 mm, 50 μm. SEM: Scanning electron microscope.
Electrical properties of sensing circuits based on the liquid metal slurry
Next, we prepared test samples with the same sensing circuit as the strain-sensing glove by scraping liquid metal slurries on the polystyrene-block-poly (ethylene butylene)-block-polystyrene(SEBS) substrate to explore its electrical performance in different test types. We designed four types of tests based on the possible application scenarios of the strain-sensing glove, including stretching, twisting, bending, and heating, as shown in Figure 3A. First, we tested the resistance changes of the strain-sensing circuit under five different tensile strains, and the normalized resistance change curves in Figure 3B show that its response capability to tensile strains in some common ranges can fully meet the basic strain-sensing requirements. Compared with other soft strain sensors based on structural designs, large stretchability is an attractive advantage for liquid metal-based strain sensors. In the subsequent extreme test, we found that the sensing circuit showed a sudden increase in resistance (sensing function failed) when the strain increased to ~300%, as shown in [Supplementary Figure 4]. Afterward, we kept the test sample under five different tensile strains for a period (30 s) to complete a whole strain change cycle. The strains ranged from 0% to 100% and then back to 0%, with intervals of 20%. The normalized resistance change curve shows that the strain-sensing circuit has a good resolution for different strain states and low attenuation of sensing data [Figure 3C]. Additionally, it can effectively match the basic properties of soft strain sensors, making it suitable for providing feedback on the static strain state. Besides, the strain-sensing circuit exhibited low response delay, as the response time and relaxation time of the strain-sensing circuit are almost consistent with the time for applying strain changes [Supplementary Figure 5] In the subsequent 600 cycles of a stretch-release test with a maximum strain of 60%, the strain-sensing circuit exhibited a drop in the resistance value during an initial period [Figure 3D], which may be attributed to more sufficient mechanical activation induced by cyclic stretching operations. In general, the strain-sensing circuit based on liquid metals has good fatigue resistance and can maintain its strain response ability effectively even after undergoing long-term use cycles.
Figure 3. Performance characterization of liquid metal-based sensing circuits under different test conditions. (A) Schematic diagram of four different test methods, including stretching, twisting, bending, and heating; (B) Normalized resistance changes of liquid metal-based sensing circuit encapsulated in SEBS during stretch-release tests at five different maximum strains; (C) Normalized resistance changes of liquid metal-based sensing circuits held at different strains for 30 s; (D) Fatigue resistance characterization of the sensing circuit during 600 stretch-release cycles and its resistance changes in later stages; (E) Resistance changes of liquid metal-based sensing circuits at different twisting angles; (F) Damage resistance characterization of the sensing circuit during 500 bend-recovery cycles and resistance changes during six cycles of them; (G) Resistance changes of liquid metal-based sensing circuits under different heating temperatures.
Figure 4. Application demonstration of the strain-sensing glove in gesture monitoring and human-machine interaction. (A) Optical image of the left hand wearing a strain-sensing glove. Scale bar: 20 mm; (B) The normalized resistance of the strain-sensing glove changes as the left hand performs different gestures; (C) Schematic diagram of the human-machine interaction circuit using the strain-sensing glove as a soft controller to manipulate the machine hand; (D) The left hand, wearing a strain-sensing glove, manipulates the machine hand to perform mirrored motions. Scale bar: 50 mm.
Subsequently, we verified the tolerance and damage resistance of the strain-sensing circuit based on the possible use and storage scenarios of the strain-sensing glove. We performed a twisting deformation cycle from 0° to 270° to the test sample (interval 90°), and the resistance did not change significantly after the torsion cycle [Figure 3E], which showed that there was no obvious damage to the conductivity of the test sample during this twisting deformation process. Rigid metal conductors may produce fatal damage during continuous bending-recovery deformation, known as fatigue failure. Therefore, we conducted 500 bending-recovery cycles on the strain-sensing circuit, where the maximum compression deformation was 50%. During this period, the strain-sensing circuit exhibited good stability, with an acceptable change in normalized resistance of ~1% during one bending-recovery cycle [Figure 3F]. Finally, we heat the strain-sensing circuit to several specified temperatures to verify its tolerance to high temperatures. When the temperature rose by 100 °C, the strain-sensing circuit still showed good conductivity, and the temperature-induced resistance increase was totally acceptable [Figure 3G]. Notably, with supercooling effects[48], sensing circuits based on liquid metal slurries can still maintain good performance for the strain sensors even at
Application demonstrations of strain-sensing gloves
Compared with commercial strain sensors, sensing units of the strain-sensing glove are in situ patterned on the nitrile glove instead of being mounted on gloves using tapes or adhesives, as seen in typical commercial strain sensors. This design possesses better conformability with finger motion. All components of the strain-sensing glove, including the substrate, encapsulation, and conductive material, are intrinsically soft and stretchable, showing better compliance than commercial sensors. To verify the application performance of the strain-sensing glove fabricated by scraping the liquid metal slurry, we demonstrated it from two aspects: monitoring and manipulating. First, a volunteer wore this strain-sensing glove on the left hand, as shown in Figure 4A. The exceptional wearing comfort made the whole process as convenient as wearing a regular glove without extra help. Subsequently, the volunteer performed various hand gestures with the left hand, and we measured the resistance changes of five strain sensors on the corresponding fingers in real time throughout this process. The strain-sensing glove is integrated, meaning the motion of any joint on the finger will contribute to the tensile deformation of strain-sensing units on the nitrile glove. This enables the maximum variation range in resistance when the finger bends to make a fist. During this demonstration, six different gestures were sequentially performed, and the normalized resistance change curves corresponding to the five strain sensors are shown in Figure 4B. From the variation curves in Figure 4B, the strain-sensing glove shows good sensitivity, and even small changes in the process of gesture switching can be reflected in the curves.
Furthermore, benefiting from wearing comfort and excellent responsiveness, the strain-sensing glove shows huge application potential in human-machine interaction. For individuals who have lost limbs due to accidents or for some operations in daily life that require the coordination of left and right hands (such as snatching), it is not easy to synchronize a prosthetic limb with normal limbs. Therefore, for some simple occasions that require limb coordination, it is also beneficial to manipulate prosthetics with normal limbs to complete collaborative tasks. To this end, based on the strain-sensing glove, we demonstrated the human-machine interaction by mirroring the hand gestures of the left hand to operate the right machine hand. Figure 4C shows the schematic diagram of the human-machine interaction circuit, where the strain-sensing glove serves as a soft controller to manipulate the machine hand. The strain-sensing unit on each finger is connected in series with a fixed value resistor (Rfix) so that the resistance changes of strain-sensing units caused by finger motion can be converted into changes in voltage, which can be read by a microcontroller unit (MCU, Arduino MEGA 2560, Supplementary Figure 6). The 10-bit analog-to-digital converter (ADC) in the MCU can convert the read analog voltage signals into digital signals with an input voltage (Vin) of
Discussion
In terms of the cost of the strain-sensing glove for daily life, several factors contribute to its affordability. The disposable nitrile gloves used as substrates are inexpensive. Additionally, the encapsulation material and PVA, which serve as binders, are also very cheap and used in minimal quantities. The commercial industrial-grade liquid metal, along with its mature patterning process, also exhibits an acceptable overall cost. Moreover, the previous reports of the recovery of liquid metals from discarded electronics using NaOH solution[35,36] indicate the potential for recycling liquid metals. By crushing discarded strain-sensing gloves and soaking them in NaOH solution, the cost of the strain-sensing glove can be further reduced.
From sampled data of application demonstration, the good sensitivity of strain-sensing units can totally meet the requirement of joint motion monitoring. However, many tiny strains with important information about physical conditions in our bodies also need to be detected and visualized, such as pulses. If wearable strain sensors for detecting pulses are fabricated using the strategy proposed in this study, a potential approach introducing tiny structures into circuits could work well; that is, such rigid tiny structures may result in necking of conductive paths when stretching, producing larger changes in resistance at the same strain.
CONCLUSIONS
In summary, we have successfully developed a strain-sensing glove designed for finger gesture monitoring and manipulating a machine hand. The glove has good responsiveness to strain and provides a high level of wearing comfort. Sensing circuits of the strain-sensing glove are prepared by scraping liquid metal slurries onto a disposable nitrile glove, offering good stretchability and durability during long-term use. Subsequently, we used the strain-sensing glove to monitor different gestures, further verifying its feasibility and sensitivity in practical sensing applications. Moreover, the strain-sensing glove can also be utilized to manipulate a machine hand to perform symmetrical gestures, exhibiting its application potential as a soft controller for human-machine interaction. The liquid metal-based circuits exhibit a good combination of good strain response and low resistance value. Therefore, together with the comfortable wearability, such a strain-sensing glove holds significant promise as a wearable flexible heater for active heat management in cold environments. The manufacturing process of the strain-sensing glove is simple and low-cost, and the whole process does not involve the use of environmentally toxic chemicals that require special operating conditions. This aspect makes it highly suitable for commercial mass production and daily use.
DECLARATIONS
Authors’ contributions
Conceptualization, methodology, investigation, data acquisition and analysis, and the manuscript writing: Wu P, Yiu CK
Conceptualization: Huang X, Yao K
Methodology: Li J, Xu G, Gao Y, Chow L, Jiao Y
Investigation: Zhao G, Yang Y
Conceiving research protocol, supervising the overall work, providing resources support, and reviewing and editing the manuscript: Yu X
Availability of data and materials
Not applicable.
Financial support and sponsorship
This work was supported by the National Natural Science Foundation of China (Grants No. 62122002), Research Grants Council of the Hong Kong Special Administrative Region (Grant Nos. 21210820, 11213721, 11215722), Innovation and Technology Fund of Innovation and Technology Commission (GHP/095/20GD), City University of Hong Kong (Grants Nos. 9667221, 9240074 and 9440298), and in part by the InnoHK Project on Project 2.2-AI-based 3D ultrasound imaging algorithm at Hong Kong Center for Cerebro-Cardiovascular Health Engineering (COCHE).
Conflicts of interest
All authors declared that there are no conflicts of interest.
Ethical approval and consent to participate
Not applicable.
Consent for publication
Not applicable.
Copyright
© The Author(s) 2023.
Supplementary Materials
REFERENCES
1. Rogers JA, Someya T, Huang Y. Materials and mechanics for stretchable electronics. Science 2010;327:1603-7.
2. Ray TR, Choi J, Bandodkar AJ, et al. Bio-Integrated wearable systems: a comprehensive review. Chem Rev 2019;119:5461-533.
3. Luo Y, Abidian MR, Ahn JH, et al. Technology roadmap for flexible sensors. ACS Nano 2023;17:5211-95.
4. Yao K, Yang Y, Wu P, Zhao G, Wang L, Yu X. Recent advances in materials, designs and applications of skin electronics. IEEE Open J Nanotechnol 2023;4:55-70.
5. Patel S, Ershad F, Zhao M, et al. Wearable electronics for skin wound monitoring and healing. Soft Sci 2022;2:9.
6. Huang X, Liu Y, Park W, et al. Intelligent soft sweat sensors for the simultaneous healthcare monitoring and safety warning. Adv Healthc Mater 2023;12:e2202846.
7. Song E, Xie Z, Bai W, et al. Miniaturized electromechanical devices for the characterization of the biomechanics of deep tissue. Nat Biomed Eng 2021;5:759-71.
8. Wu P, Zhou L, Lv S, Fu J, He Y. Self-sintering liquid metal ink with LAPONITE® for flexible electronics. J Mater Chem C 2021;9:3070-80.
9. Wang B, Thukral A, Xie Z, et al. Flexible and stretchable metal oxide nanofiber networks for multimodal and monolithically integrated wearable electronics. Nat Commun 2020;11:2405.
10. Yu X, Xie Z, Yu Y, et al. Skin-integrated wireless haptic interfaces for virtual and augmented reality. Nature 2019;575:473-9.
11. Li D, Zhou J, Yao K, et al. Touch IoT enabled by wireless self-sensing and haptic-reproducing electronic skin. Sci Adv 2022;8:eade2450.
12. Chen M, Ouyang J, Jian A, et al. Imperceptible, designable, and scalable braided electronic cord. Nat Commun 2022;13:7097.
13. Souri H, Banerjee H, Jusufi A, et al. Wearable and stretchable strain sensors: materials, sensing mechanisms, and applications. Adv Intell Syst-Ger 2020;2:2000039.
14. Shen Z, Liu F, Huang S, et al. Progress of flexible strain sensors for physiological signal monitoring. Biosens Bioelectron 2022;211:114298.
15. Liao X, Zhang Z, Kang Z, Gao F, Liao Q, Zhang Y. Ultrasensitive and stretchable resistive strain sensors designed for wearable electronics. Mater Horiz 2017;4:502-10.
16. Kim SR, Kim JH, Park JW. Wearable and transparent capacitive strain sensor with high sensitivity based on patterned ag nanowire networks. ACS Appl Mater Interfaces 2017;9:26407-16.
17. Lu C, Chen J, Jiang T, Gu G, Tang W, Wang ZL. A stretchable, flexible triboelectric nanogenerator for self-powered real-time motion monitoring. Adv Mater Technol 2018;3:1800021.
18. Huo Z, Wang X, Zhang Y, et al. High-performance Sb-doped p-ZnO NW films for self-powered piezoelectric strain sensors. Nano Energy 2020;73:104744.
19. Wong TH, Yiu CK, Zhou J, et al. Tattoo-like epidermal electronics as skin sensors for human machine interfaces. Soft Sci 2021;1:10.
20. Wang R, Sun L, Zhu X, et al. Carbon nanotube-based strain sensors: structures, fabrication, and applications. Adv Mater Technol 2023;8:2200855.
21. Basarir F, Madani Z, Vapaavuori J. Recent advances in silver nanowire based flexible capacitive pressure sensors: from structure, fabrication to emerging applications. Adv Mater Inter 2022;9:2200866.
22. Baharfar M, Kalantar-Zadeh K. Emerging role of liquid metals in sensing. ACS Sens 2022;7:386-408.
23. Li G, Li C, Li G, et al. Development of conductive hydrogels for fabricating flexible strain sensors. Small 2022;18:e2101518.
25. Zhang M, Yao S, Rao W, Liu J. Transformable soft liquid metal micro/nanomaterials. Mat Sci Eng R 2019;138:1-35.
26. Ma J, Krisnadi F, Vong MH, Kong M, Awartani OM, Dickey MD. Shaping a soft future: patterning liquid metals. Adv Mater 2023;35:e2205196.
27. Park YG, Lee GY, Jang J, Yun SM, Kim E, Park JU. Liquid metal-based soft electronics for wearable healthcare. Adv Healthc Mater 2021;10:e2002280.
28. Khoshmanesh K, Tang SY, Zhu JY, et al. Liquid metal enabled microfluidics. Lab Chip 2017;17:974-93.
29. Wu P, Wang Z, Yao X, Fu J, He Y. Recyclable conductive nanoclay for direct in situ printing flexible electronics. Mater Horiz 2021;8:2006-17.
30. Neumann TV, Dickey MD. Liquid Metal direct write and 3d printing: a review. Adv Mater Technol 2020;5:2000070.
31. Li X, Li M, Zong L, et al. Liquid metal droplets wrapped with polysaccharide microgel as biocompatible aqueous ink for flexible conductive devices. Adv Funct Mater 2018;28:1804197.
32. Mohammed MG, Kramer R. All-printed flexible and stretchable electronics. Adv Mater 2017;29:1604965.
33. Tang L, Mou L, Zhang W, Jiang X. Large-scale fabrication of highly elastic conductors on a broad range of surfaces. ACS Appl Mater Interfaces 2019;11:7138-47.
34. Tang L, Cheng S, Zhang L, et al. Printable metal-polymer conductors for highly stretchable bio-devices. iScience 2018;4:302-11.
35. Xu J, Guo H, Ding H, et al. Printable and recyclable conductive ink based on a liquid metal with excellent surface wettability for flexible electronics. ACS Appl Mater Interfaces 2021;13:7443-52.
36. Wu P, Fu J, Xu Y, He Y. Liquid metal microgels for three-dimensional printing of smart electronic clothes. ACS Appl Mater Interfaces 2022;14:13458-67.
37. Lin Y, Genzer J, Dickey MD. Attributes, fabrication, and applications of gallium-based liquid metal particles. Adv Sci 2020;7:2000192.
38. Markvicka EJ, Bartlett MD, Huang X, Majidi C. An autonomously electrically self-healing liquid metal-elastomer composite for robust soft-matter robotics and electronics. Nat Mater 2018;17:618-24.
39. Wang S, Nie Y, Zhu H, et al. Intrinsically stretchable electronics with ultrahigh deformability to monitor dynamically moving organs. Sci Adv 2022;8:eabl5511.
40. Ozutemiz KB, Wissman J, Ozdoganlar OB, Majidi C. EGain-metal interfacing for liquid metal circuitry and microelectronics integration. Adv Mater Interfaces 2018;5:1701596.
41. Liao M, Liao H, Ye J, Wan P, Zhang L. Polyvinyl alcohol-stabilized liquid metal hydrogel for wearable transient epidermal sensors. ACS Appl Mater Interfaces 2019;11:47358-64.
42. Hu G, Wang S, Yu J, Zhang J, Sun Y, Kong D. A facile and scalable patterning approach for ultrastretchable liquid metal features. Lab Chip 2022;22:4933-40.
43. Park YG, An HS, Kim JY, Park JU. High-resolution, reconfigurable printing of liquid metals with three-dimensional structures. Sci Adv 2019;5:eaaw2844.
44. Boley JW, White EL, Kramer RK. Mechanically sintered gallium-indium nanoparticles. Adv Mater 2015;27:2355-60.
45. Chang H, Zhang P, Guo R, et al. Recoverable liquid metal paste with reversible rheological characteristic for electronics printing. ACS Appl Mater Interfaces 2020;12:14125-35.
46. Thrasher CJ, Farrell ZJ, Morris NJ, Willey CL, Tabor CE. Mechanoresponsive polymerized liquid metal networks. Adv Mater 2019;31:e1903864.
47. Kazem N, Hellebrekers T, Majidi C. Soft multifunctional composites and emulsions with liquid metals. Adv Mater 2017;29:1605985.
Cite This Article
Export citation file: BibTeX | RIS
OAE Style
Wu P, Yiu CK, Huang X, Li J, Xu G, Gao Y, Yao K, Chow L, Zhao G, Yang Y, Jiao Y, Yu X. Liquid metal-based strain-sensing glove for human-machine interaction. Soft Sci 2023;3:35. http://dx.doi.org/10.20517/ss.2023.26
AMA Style
Wu P, Yiu CK, Huang X, Li J, Xu G, Gao Y, Yao K, Chow L, Zhao G, Yang Y, Jiao Y, Yu X. Liquid metal-based strain-sensing glove for human-machine interaction. Soft Science. 2023; 3(4): 35. http://dx.doi.org/10.20517/ss.2023.26
Chicago/Turabian Style
Wu, Pengcheng, Chun Ki Yiu, Xingcan Huang, Jiyu Li, Guoqiang Xu, Yuyu Gao, Kuanming Yao, Lung Chow, Guangyao Zhao, Yawen Yang, Yanli Jiao, Xinge Yu. 2023. "Liquid metal-based strain-sensing glove for human-machine interaction" Soft Science. 3, no.4: 35. http://dx.doi.org/10.20517/ss.2023.26
ACS Style
Wu, P.; Yiu CK.; Huang X.; Li J.; Xu G.; Gao Y.; Yao K.; Chow L.; Zhao G.; Yang Y.; Jiao Y.; Yu X. Liquid metal-based strain-sensing glove for human-machine interaction. Soft. Sci. 2023, 3, 35. http://dx.doi.org/10.20517/ss.2023.26
About This Article
Special Issue
Copyright
Data & Comments
Data
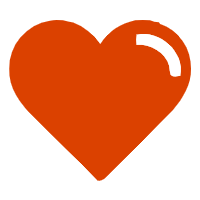

Comments
Comments must be written in English. Spam, offensive content, impersonation, and private information will not be permitted. If any comment is reported and identified as inappropriate content by OAE staff, the comment will be removed without notice. If you have any queries or need any help, please contact us at support@oaepublish.com.